Note: As before, thanks to Bradley Rothenberg (of nTopology) and Ryan Schmidt (of MeshMixer/Autodesk) for their continued help on this workflow.
As documented previously (1, 2, 3, 4), I've been working on a multi-step workflow to create printable lattice structures for mechanical parts. In earlier posts, I described some of the techniques I used to generate the lattice itself, and at this point I'm ready to refine the mechanical features and evaluate the end result.
I've made a few changes to my remeshed surfaces since my last post, so I start this process today in MeshMixer. Here I've got three parts: The stem body itself, a surface that's designed to reinforce the threaded portions of the faceplate bolt holes (this is mostly hidden inside the stem body, but you can see its border still), and the faceplate itself.
From this, I export three separate OBJ files and import the into nTopology Element. There, I generate simple surface lattices: each edge in the OBJ is turned into a beam in the new lattices.
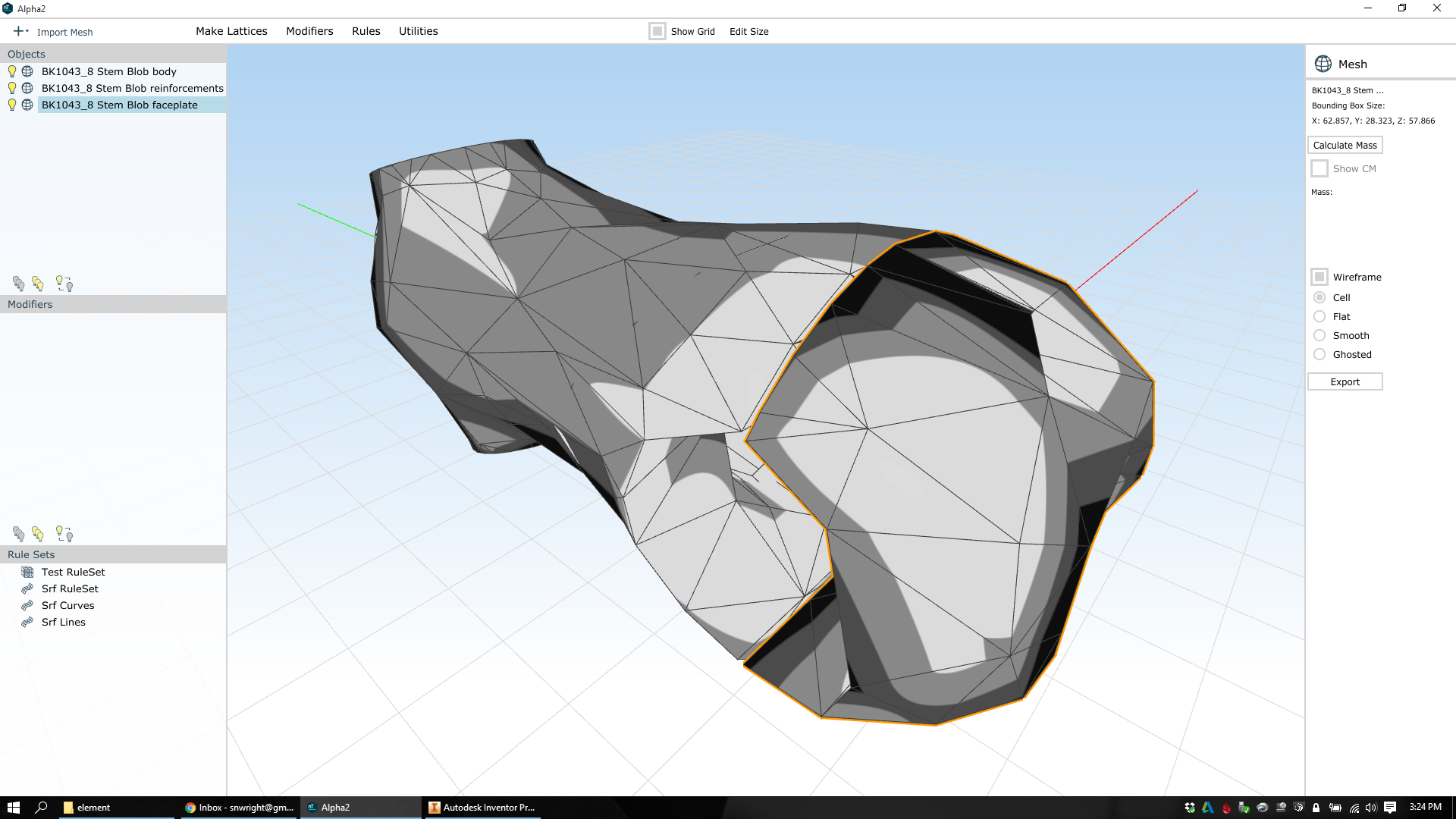
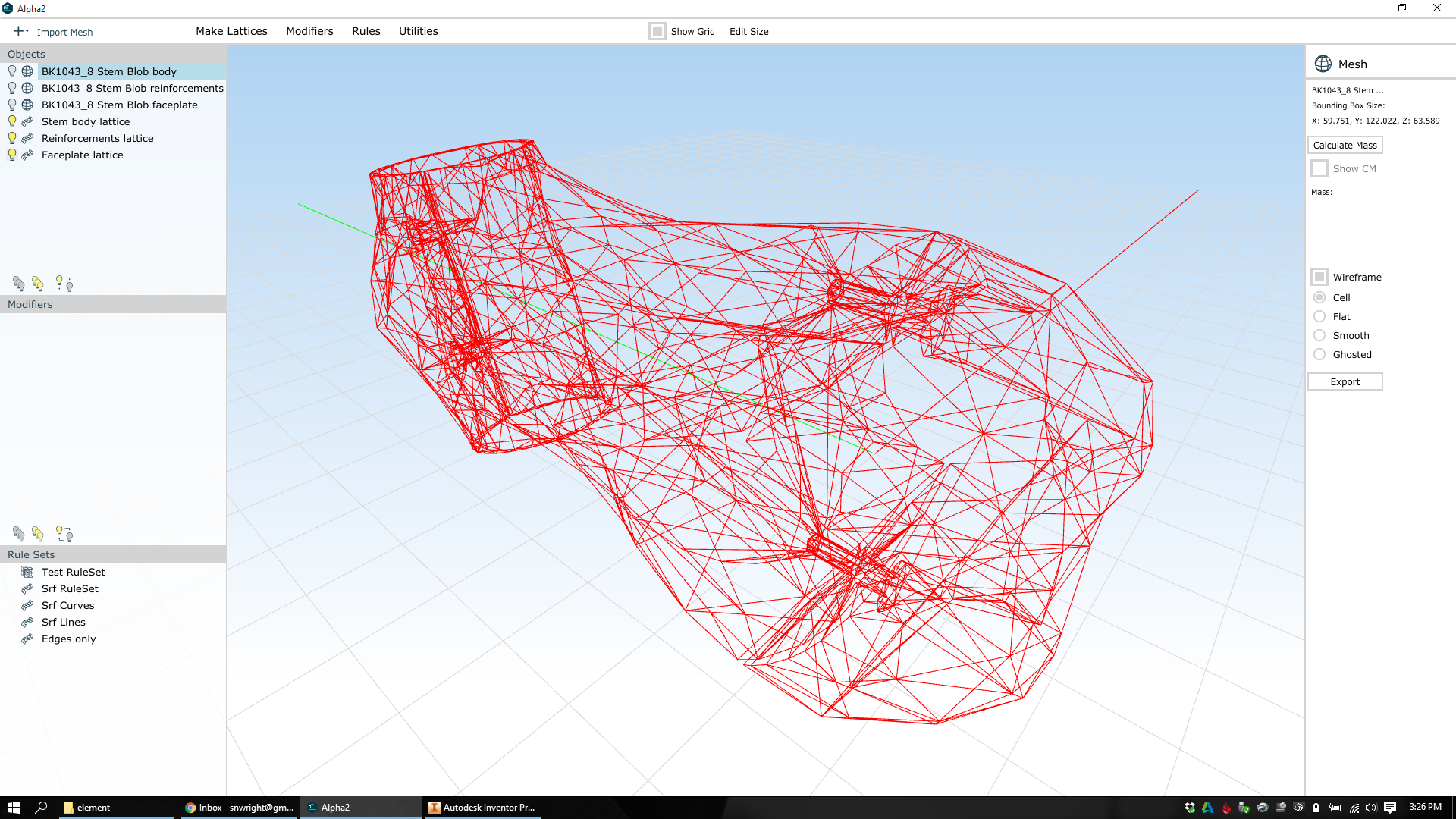
Next, I create a set of attractors that I'll use to control the thickness of my lattice. The locations of these attractors were taken directly from Inventor; I know the XYZ locations of the general areas that I want to thicken, and so put the attractors right where I want them. Then I control each attractor's size and falloff curve to thicken just the areas I want. In the shots below I have every attractor on a cosine falloff; the bolt attractors are 12mm in size, and the clamp cylinder attractors are just a few mm bigger than the diameter of the cylinder.
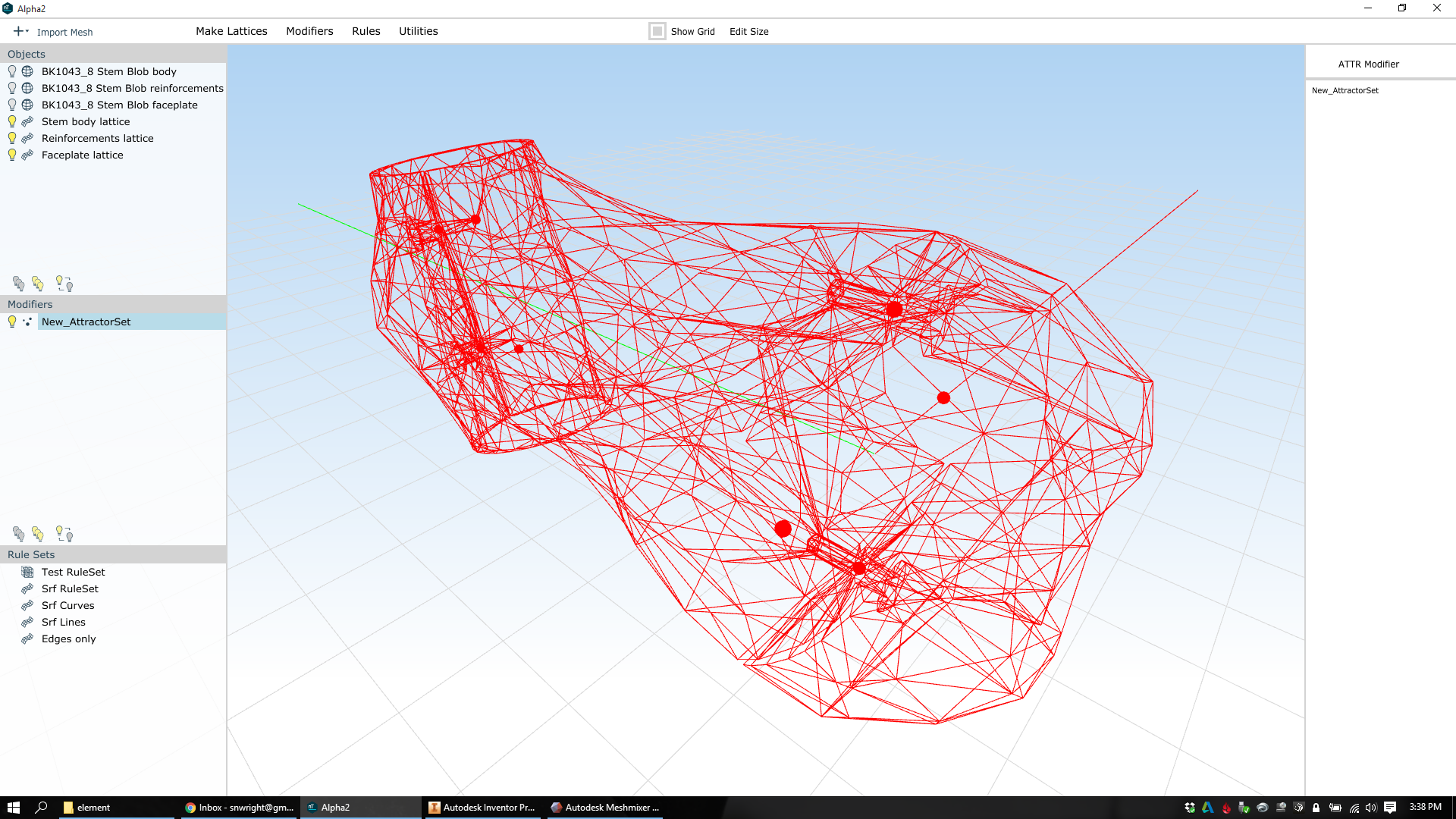
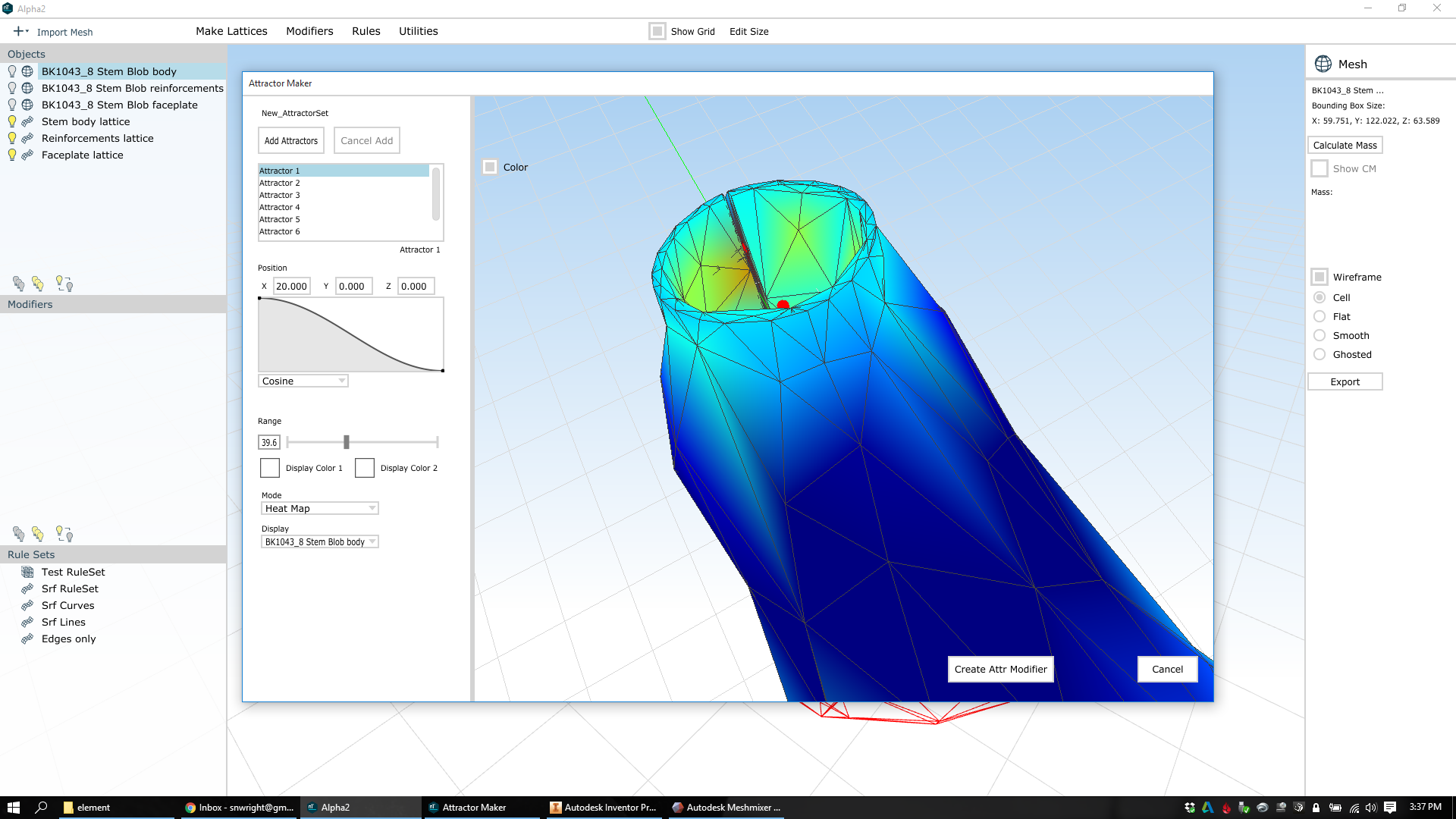
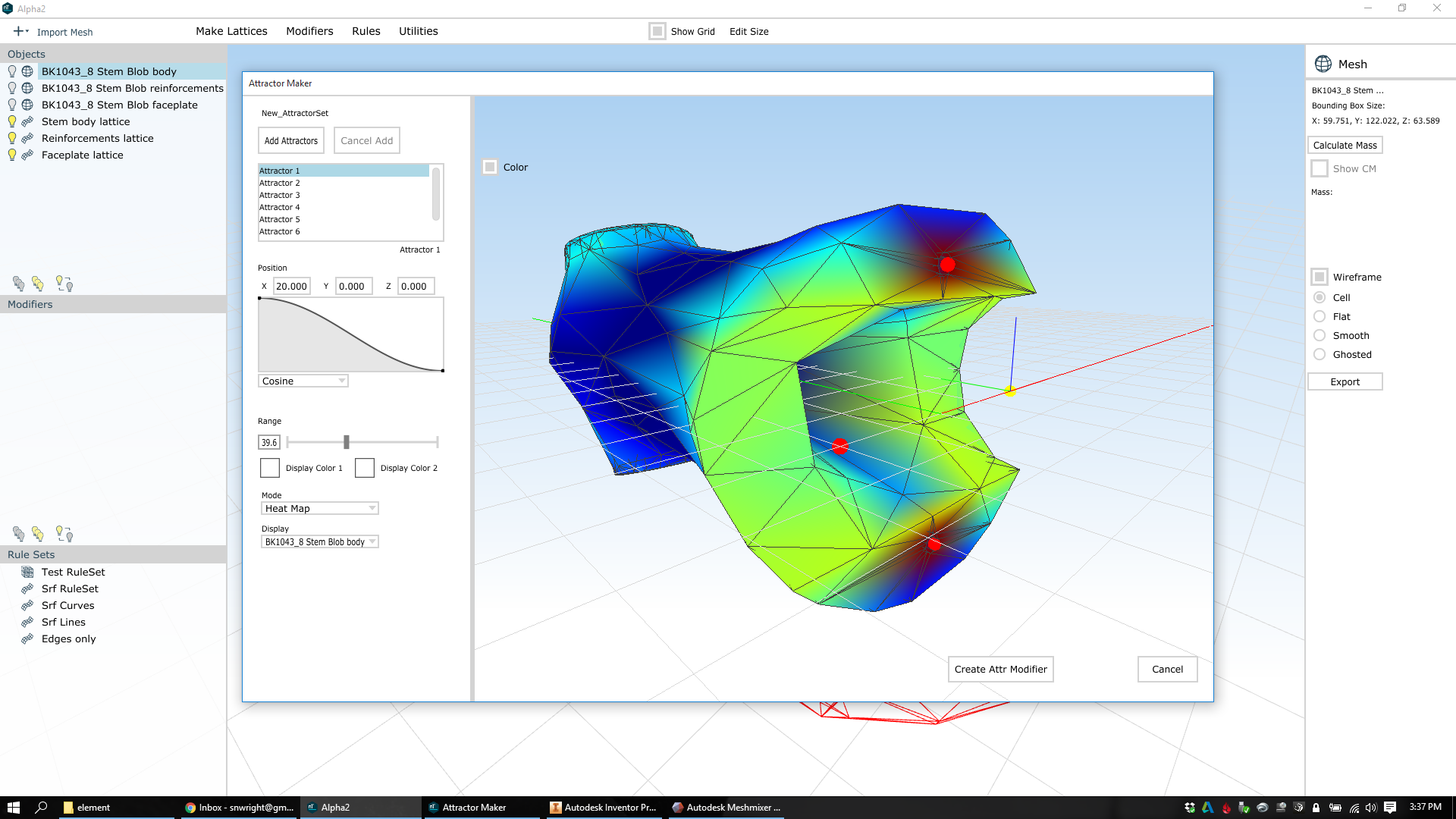
Once I've got the attractors set up, I go through each part and thicken the lattice. The grey appearance is just where nTopology is showing me a wireframe, and the density of the mesh is really high:
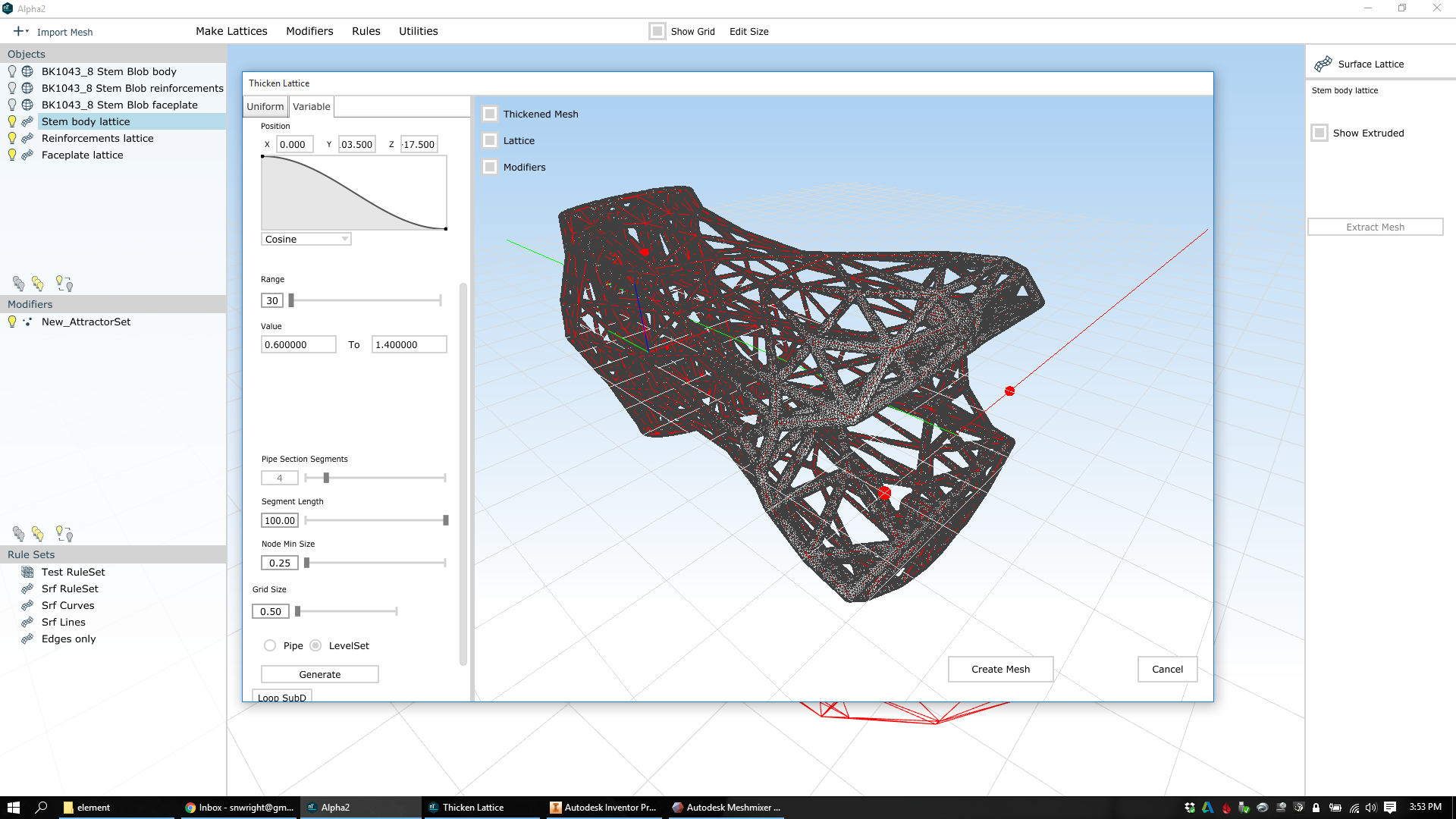
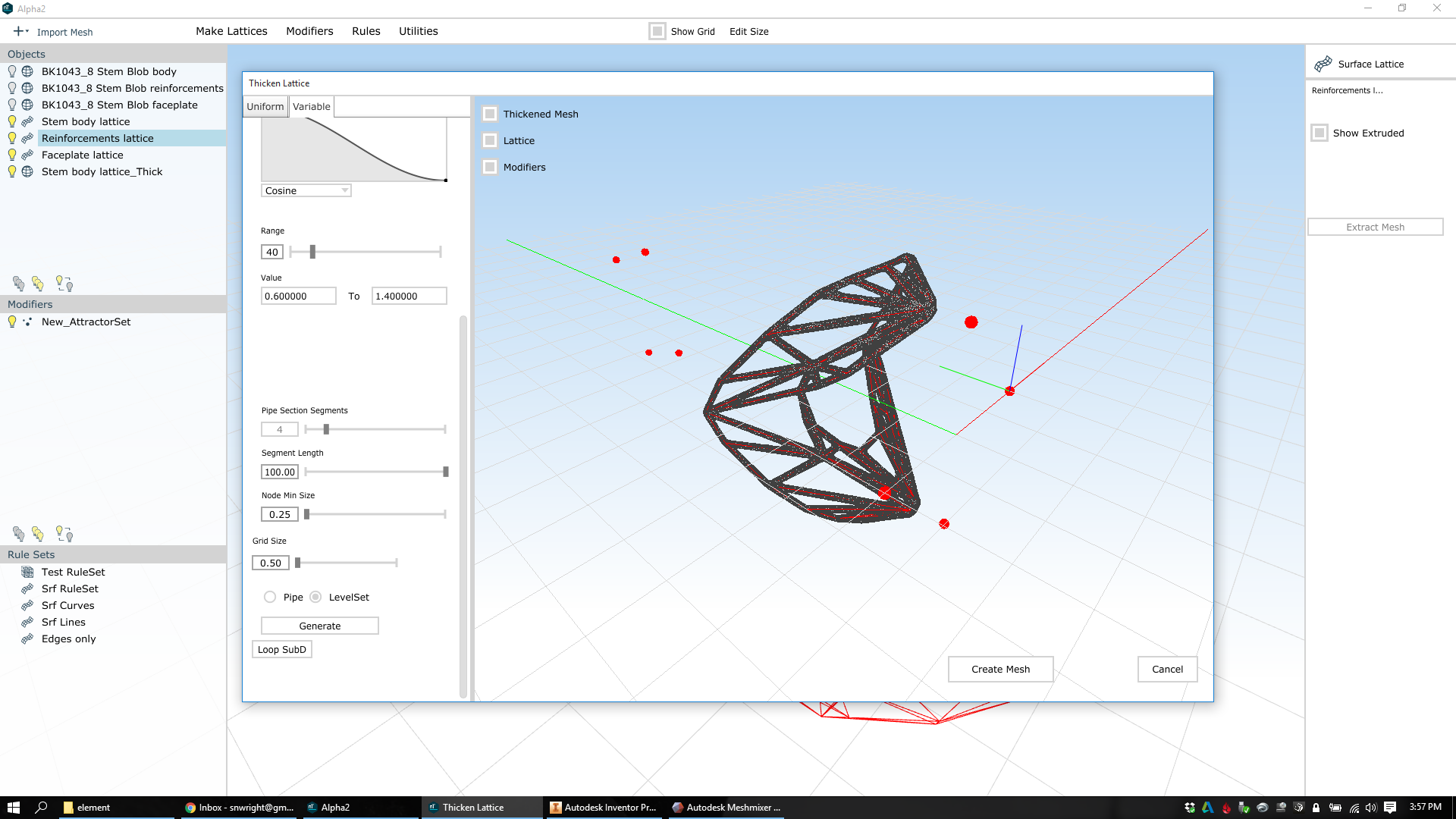
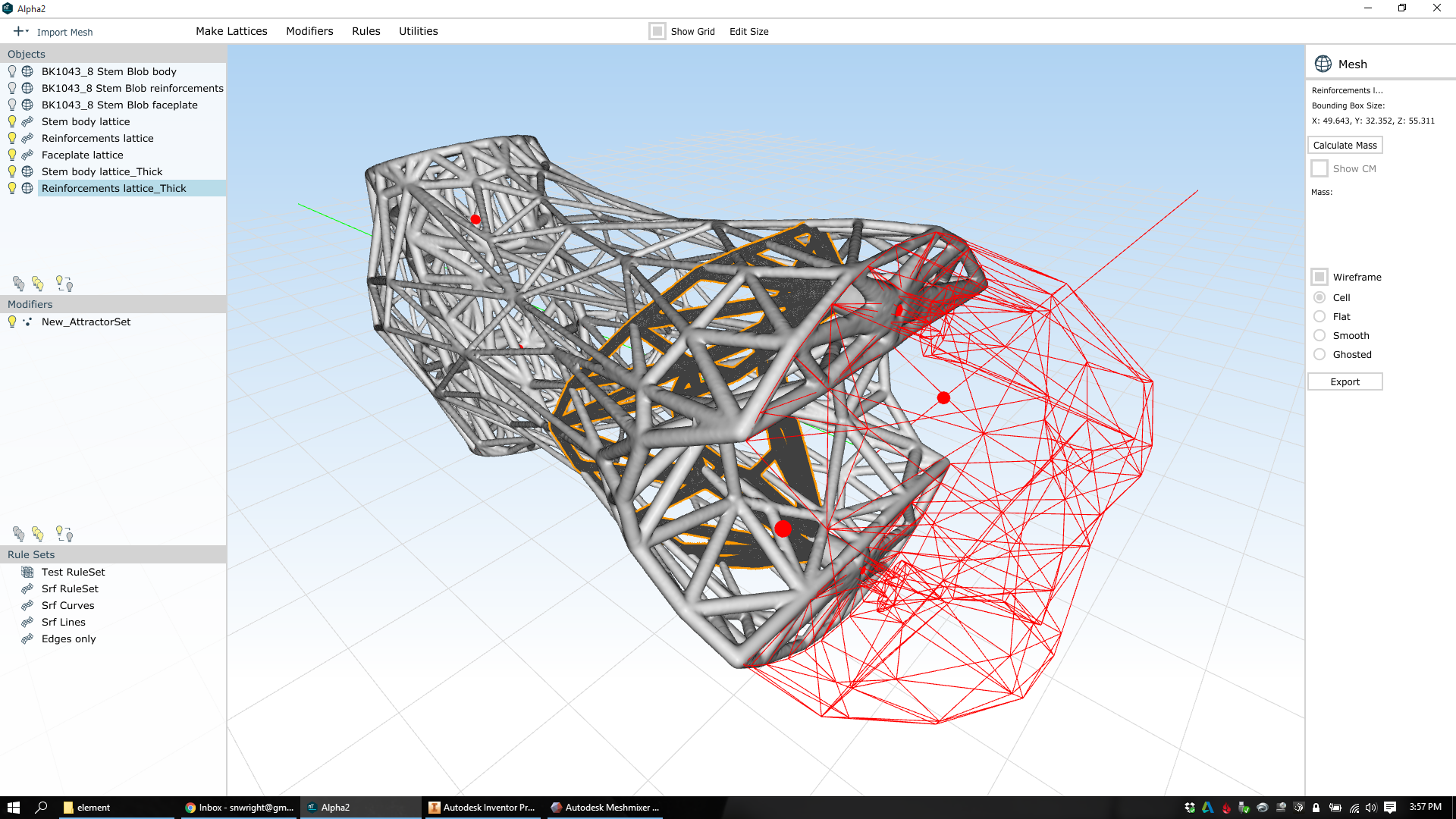
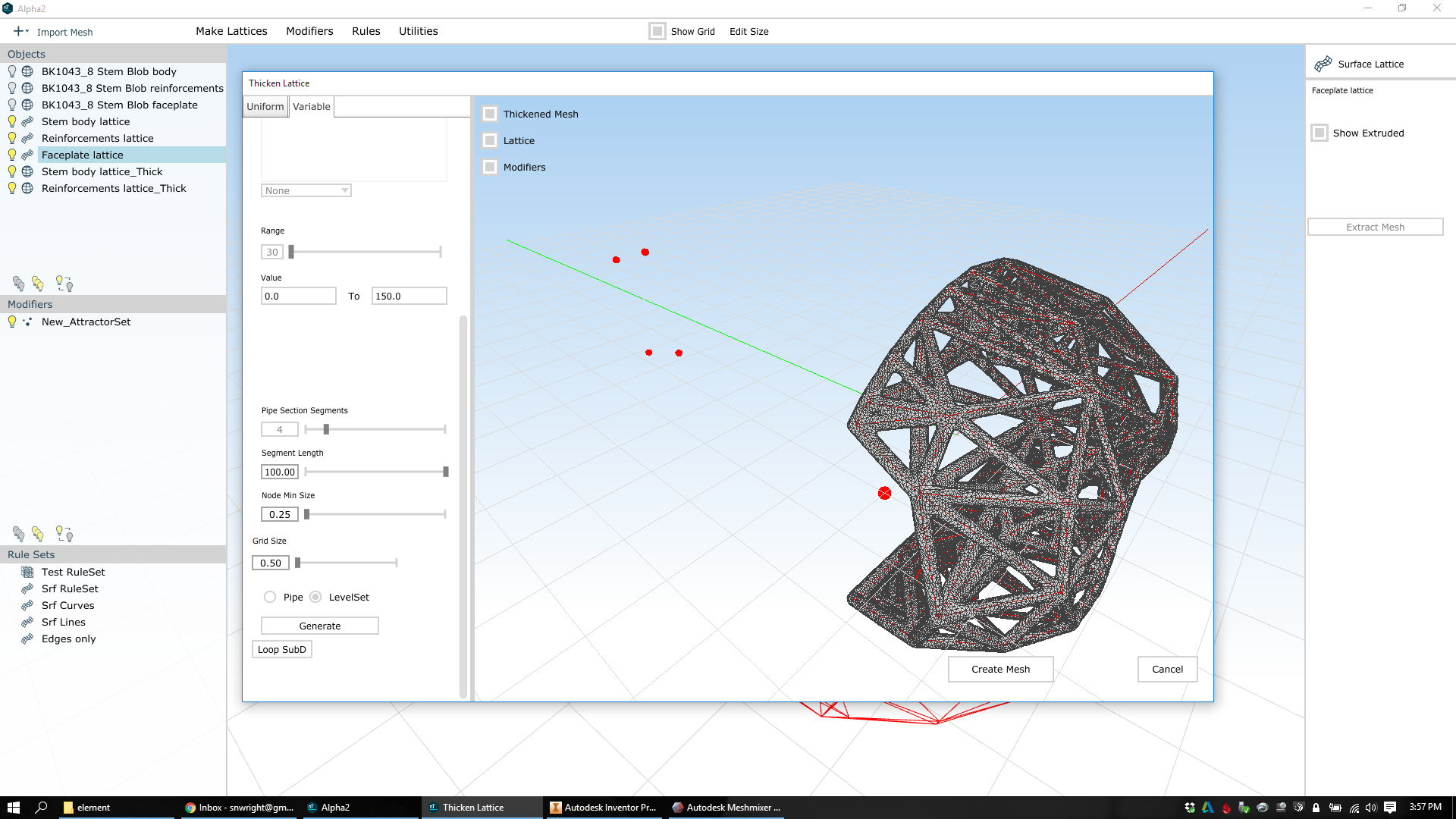
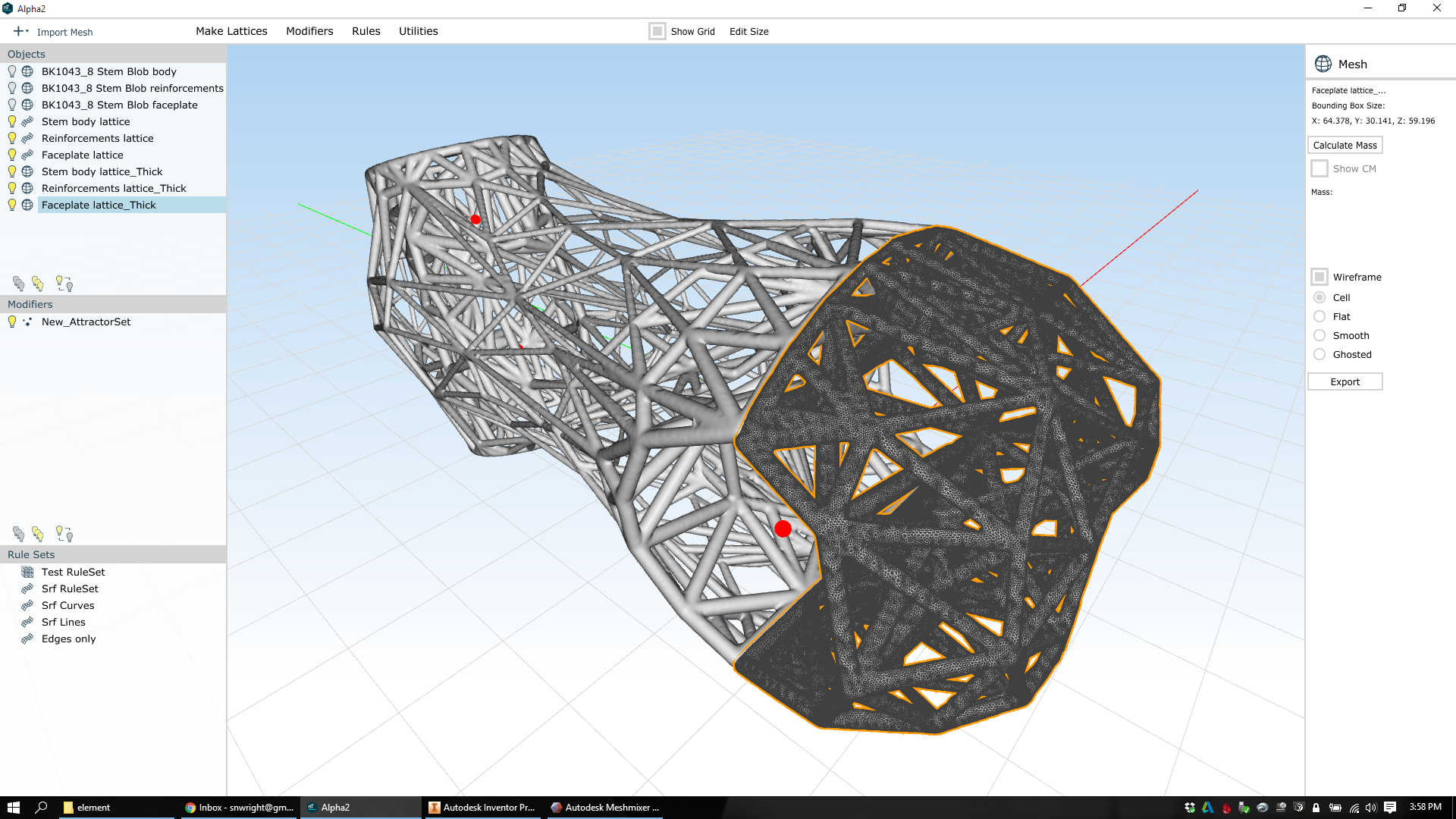
You can see here that each part has some degree of variation in its beam sizes. In the bolt areas the mesh is dense and the beams are thick; in the middle of the stem body the mesh is sparse and the beams are thin.
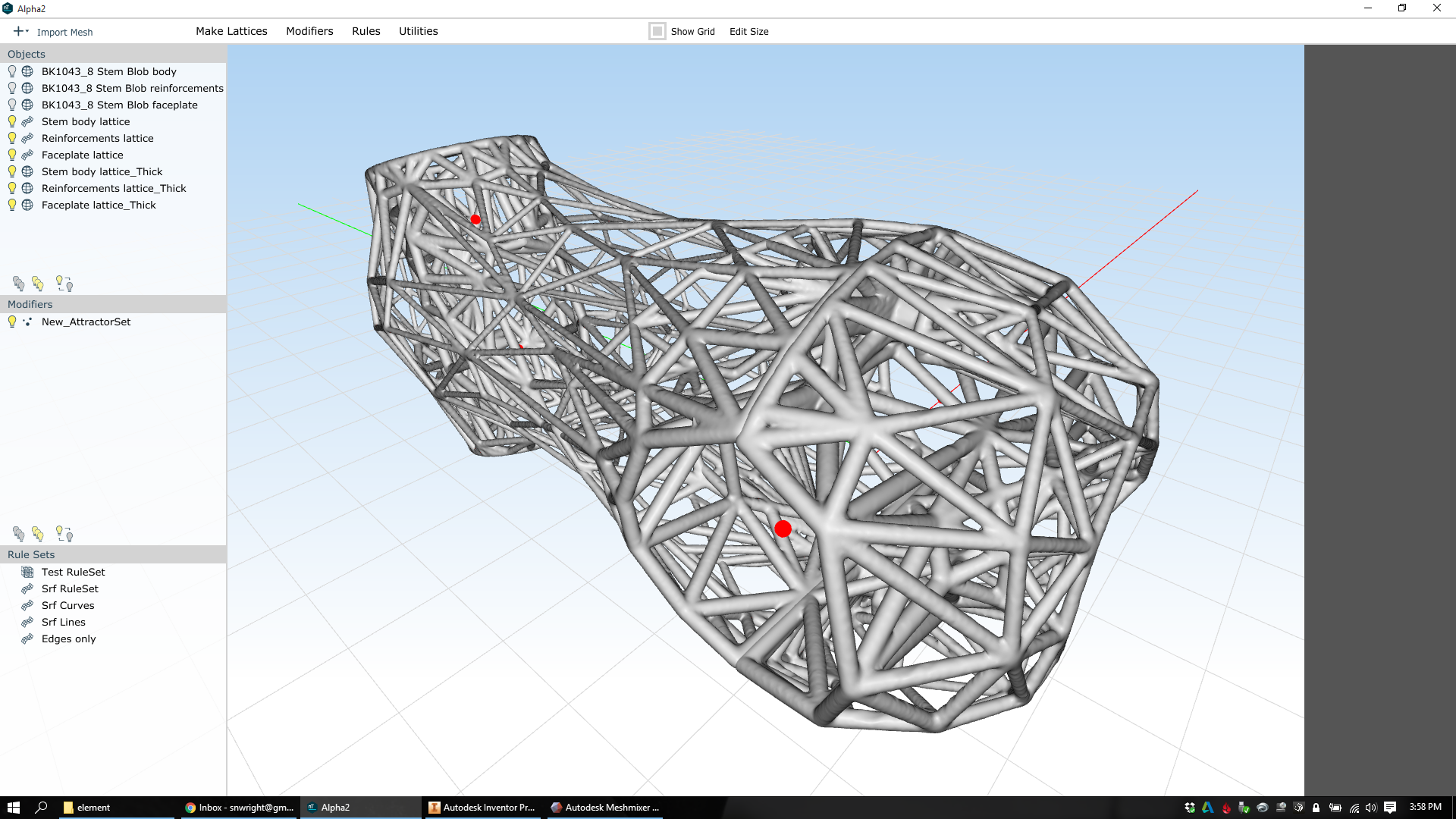
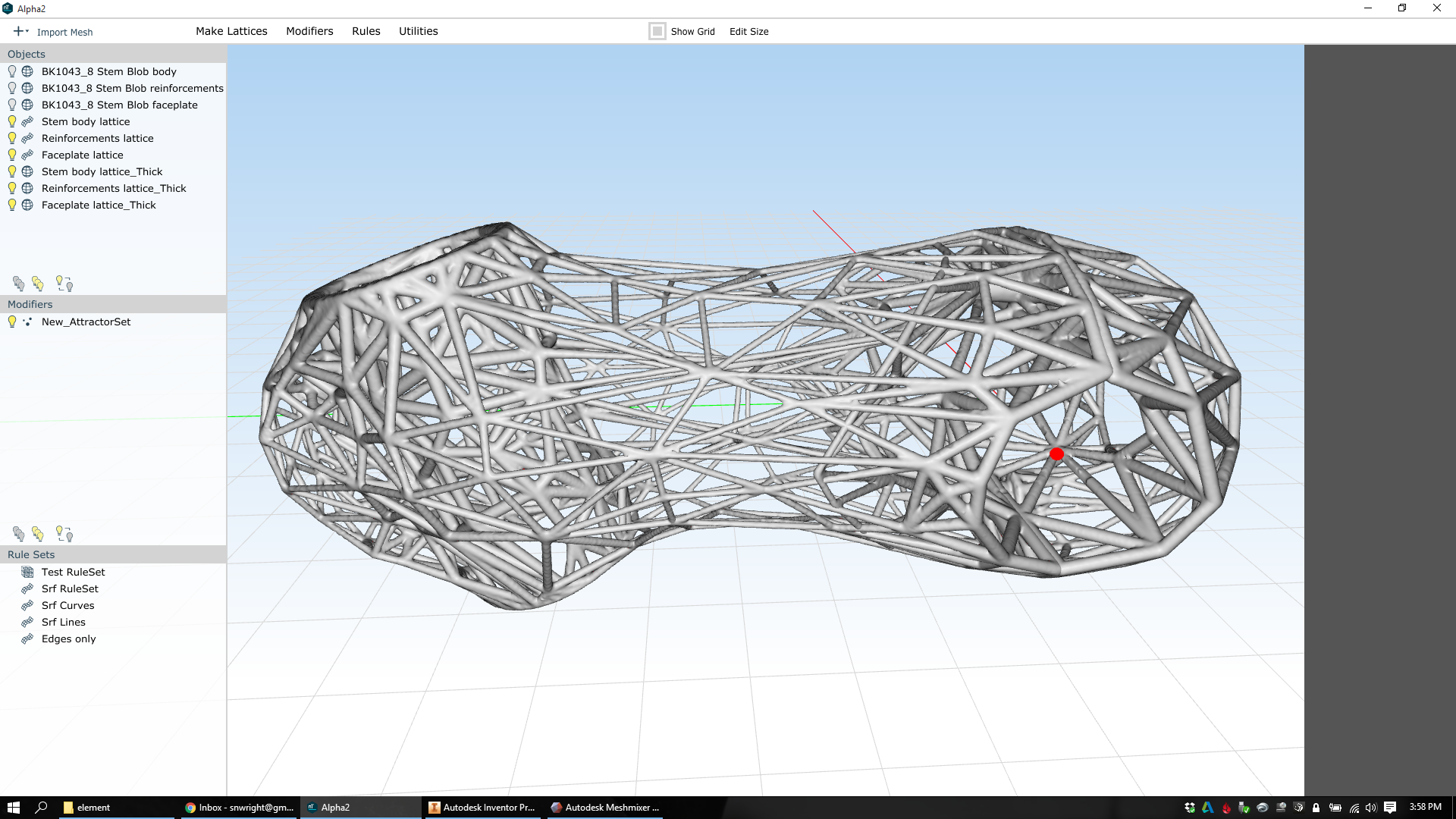
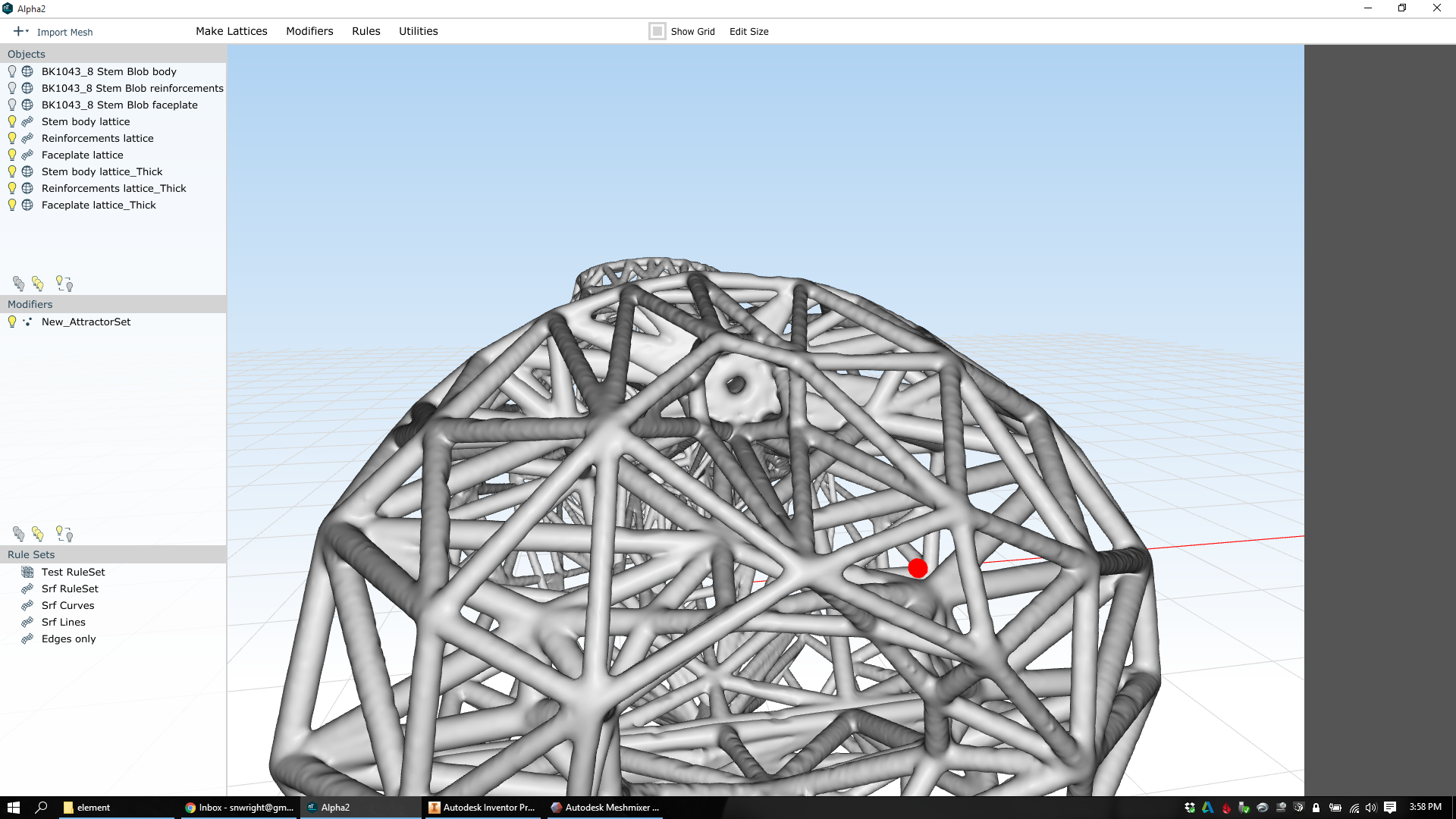
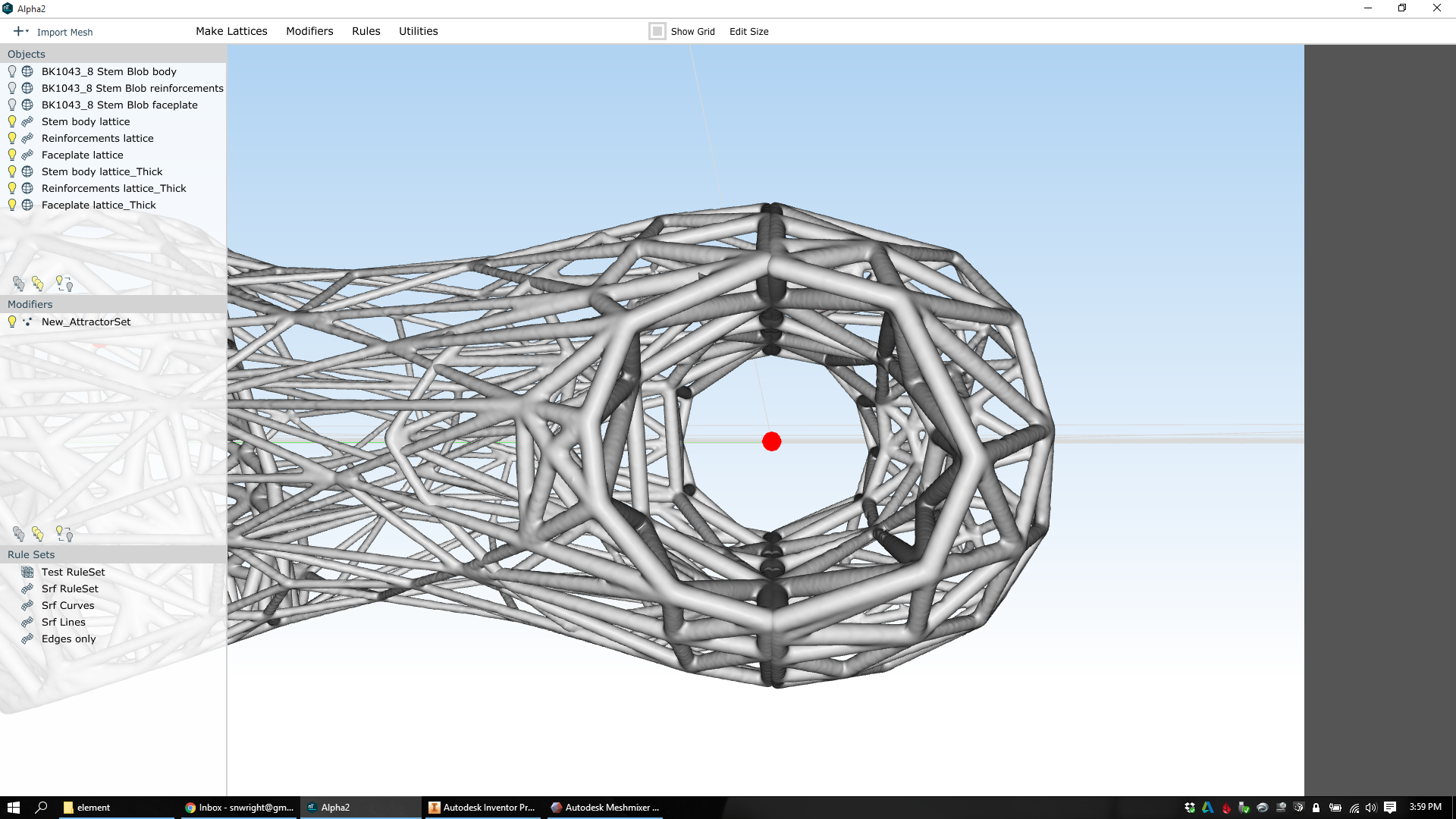
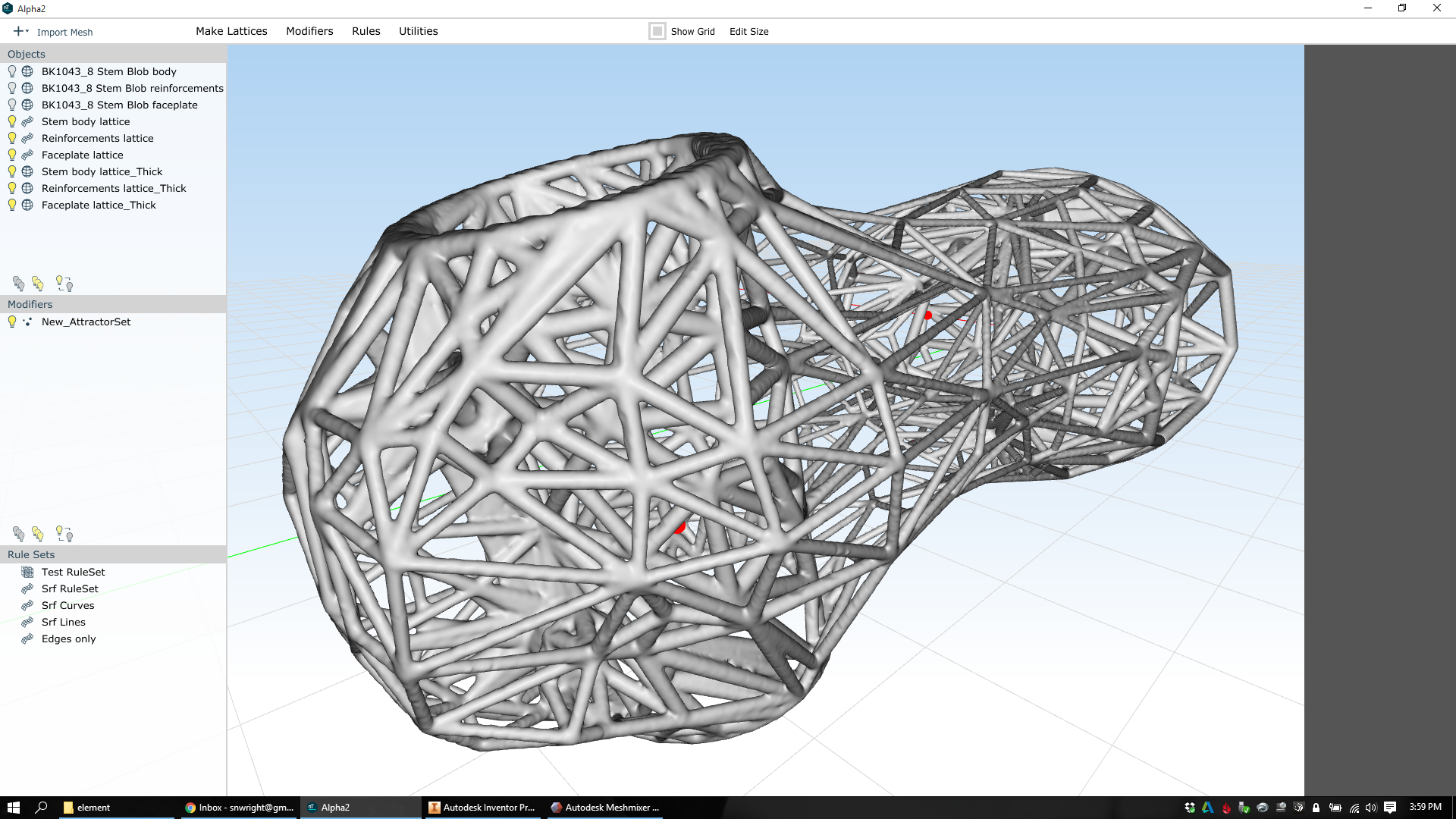
At this point, I export each of the three lattices and bring them back into MeshMixer. Here you can see them overlaid on the original meshes:
Now, I import meshes that correspond with the mechanical features I want to preserve in the part. I've taken these directly from Inventor: I created an assembly file containing the original IPT and then created a new IPT that refers directly to the mechanical features. I export that as an STL, bring it into MeshMixer, and then select it and flip all of its normals so that it's inside out. Here you can see those boolean parts - first as red bodies in Inventor, then as meshes in MeshMixer, then as inside-out meshes:
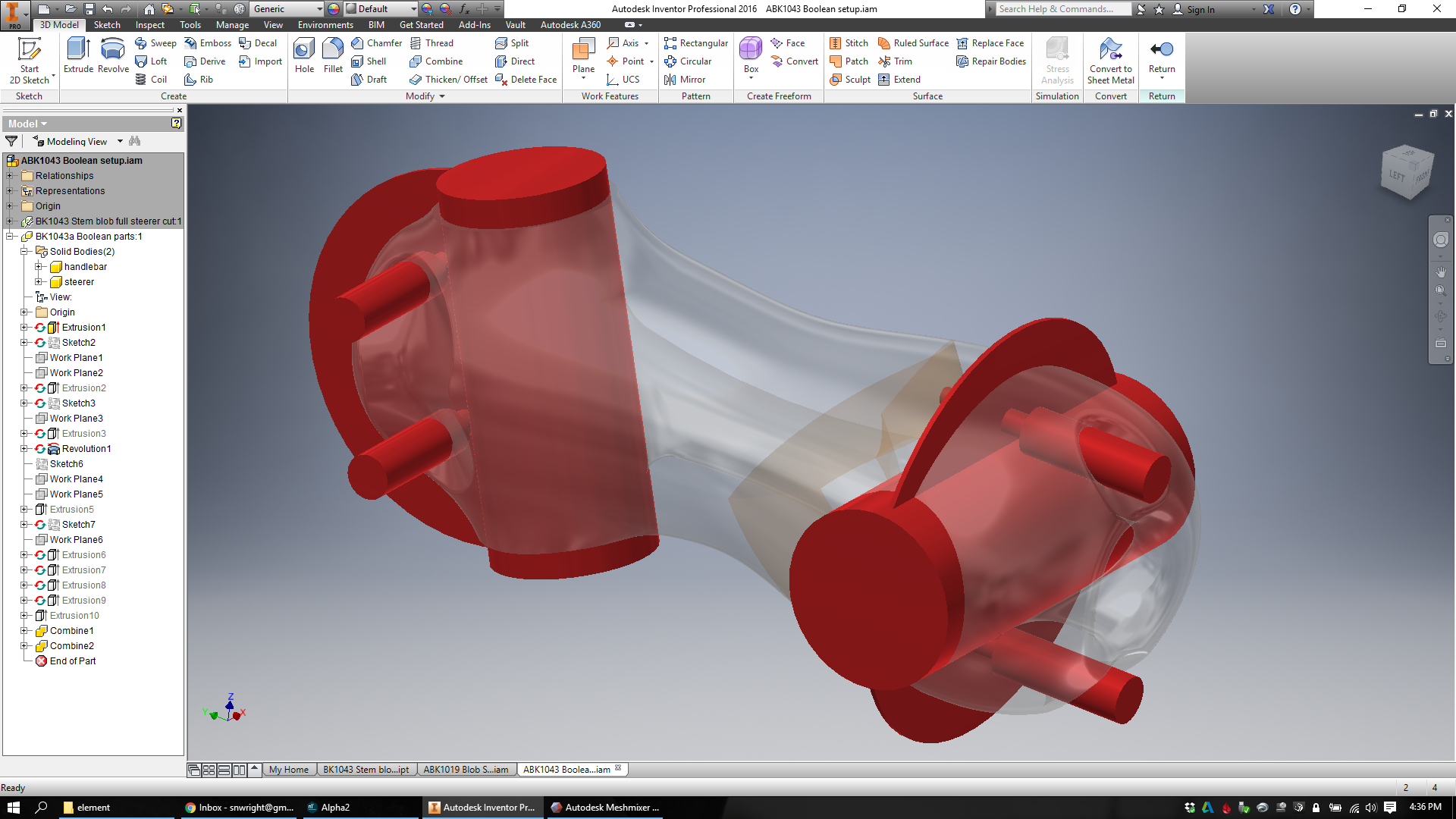
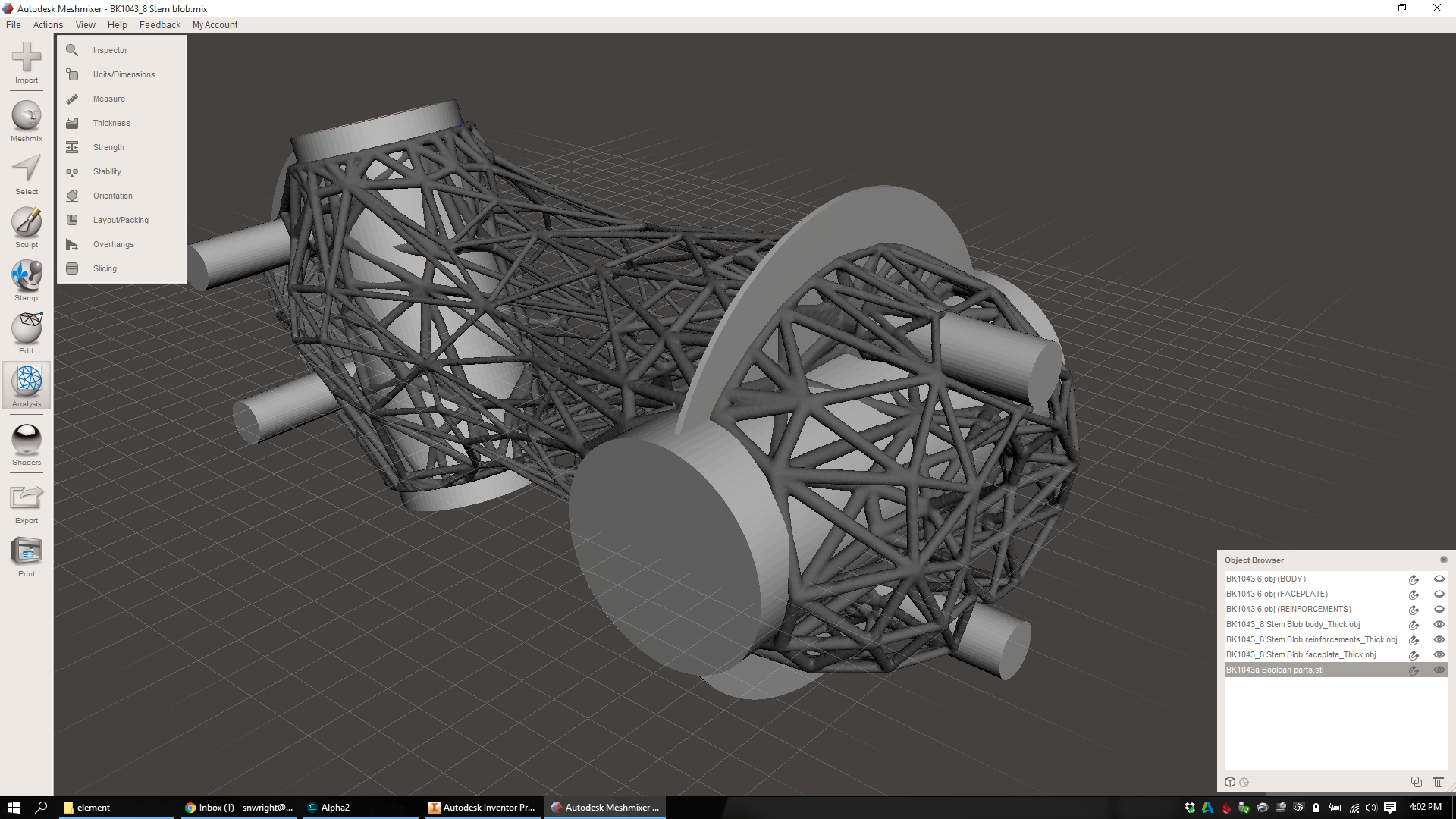
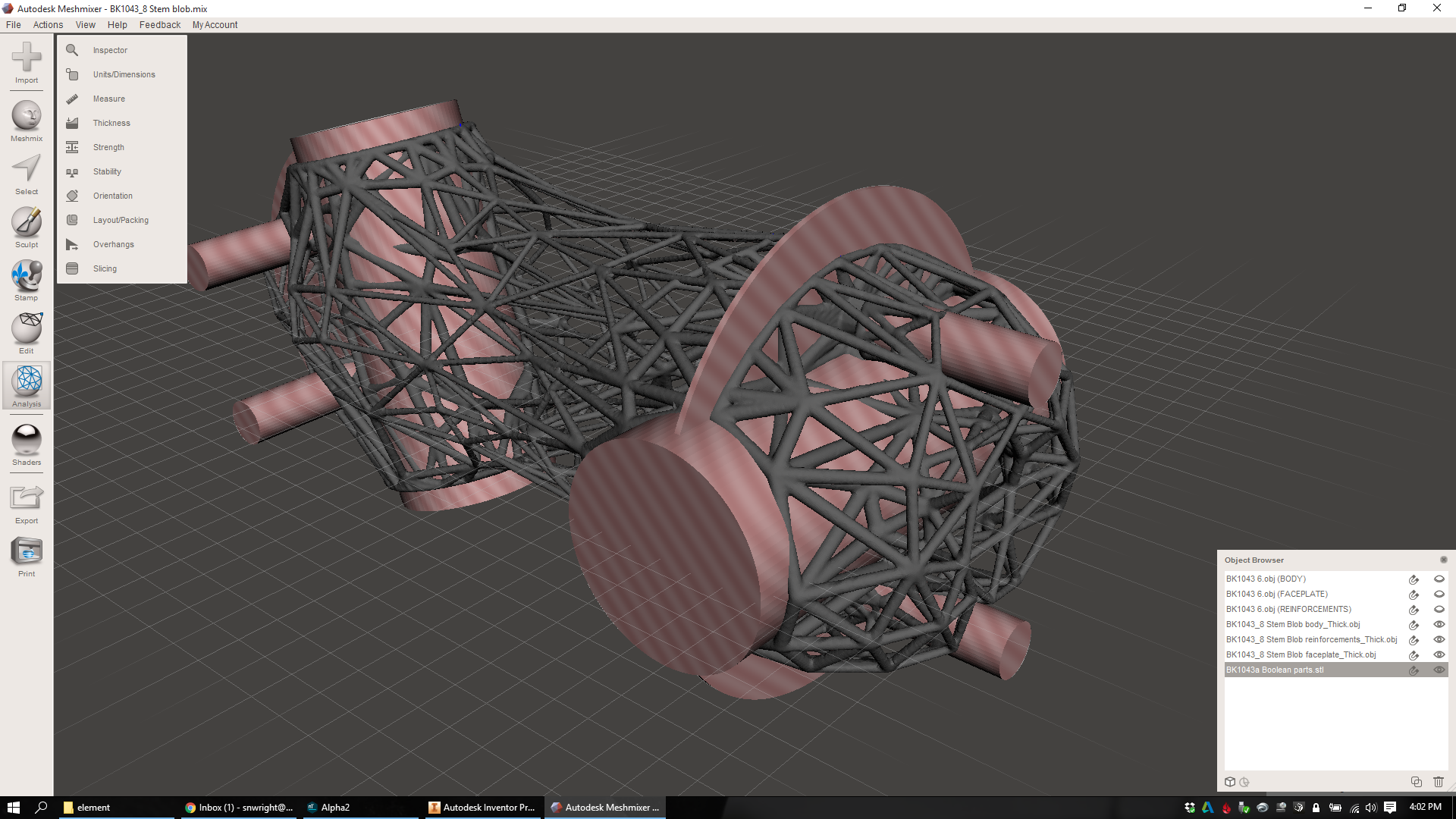
Now I select the three lattice objects, combine them into one, and run the inspector tool and fix all of the mesh problems. Then I run "Make Solid" on the whole object. I run this in "Accurate" mode and turn the "Solid Accuracy" and "Mesh Density" settings *way* up in order to keep the whole thing smooth:
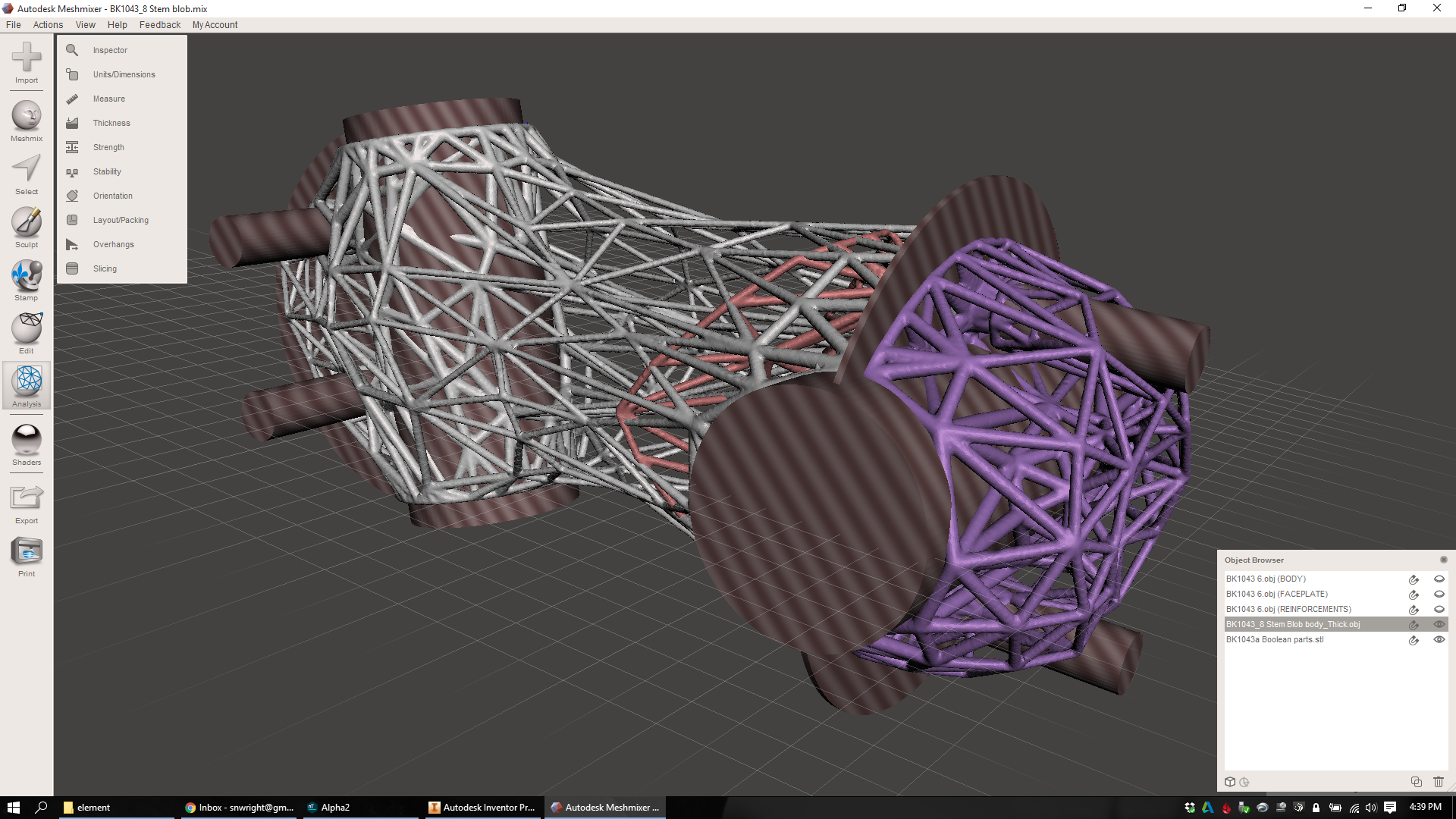
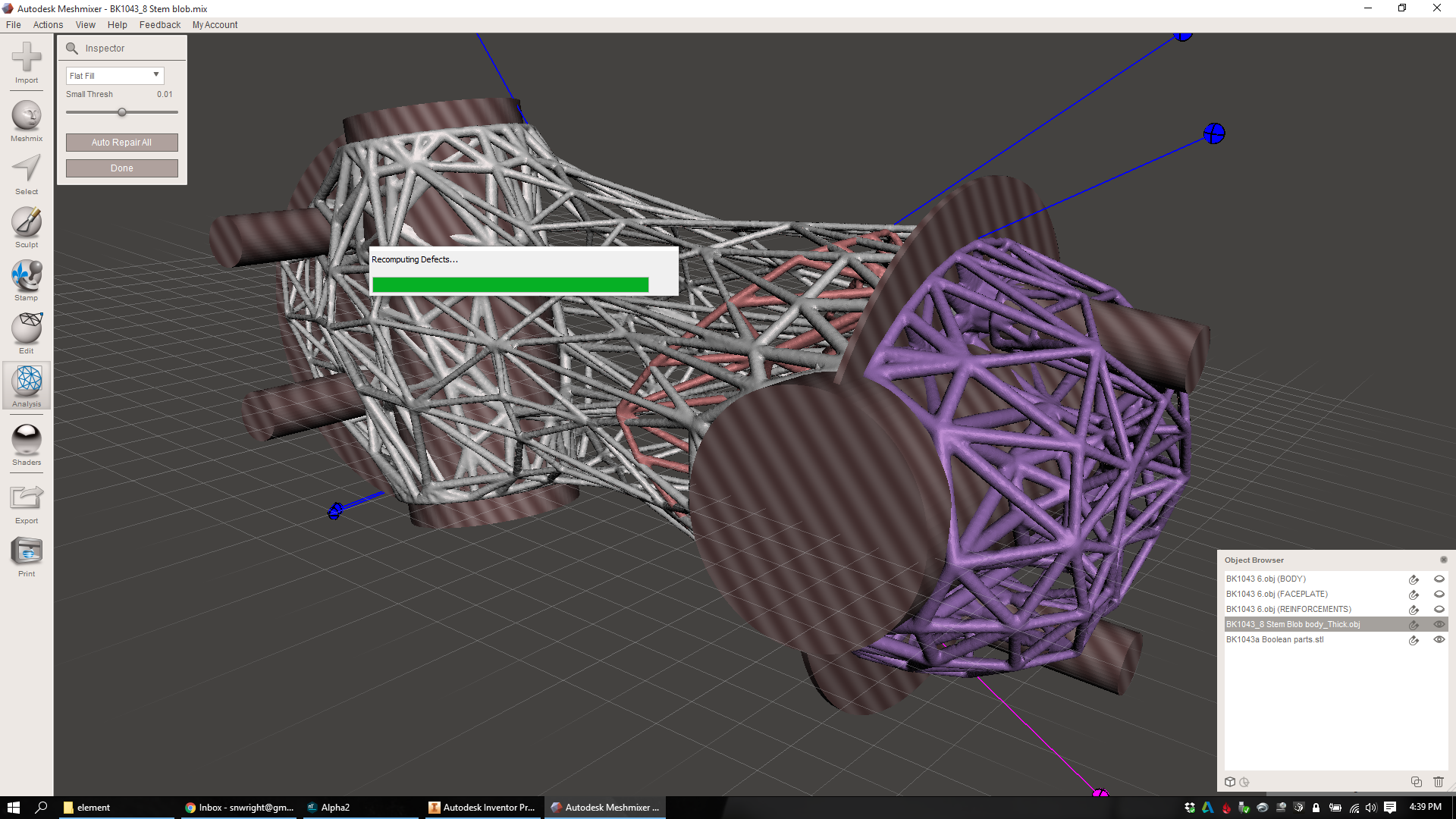
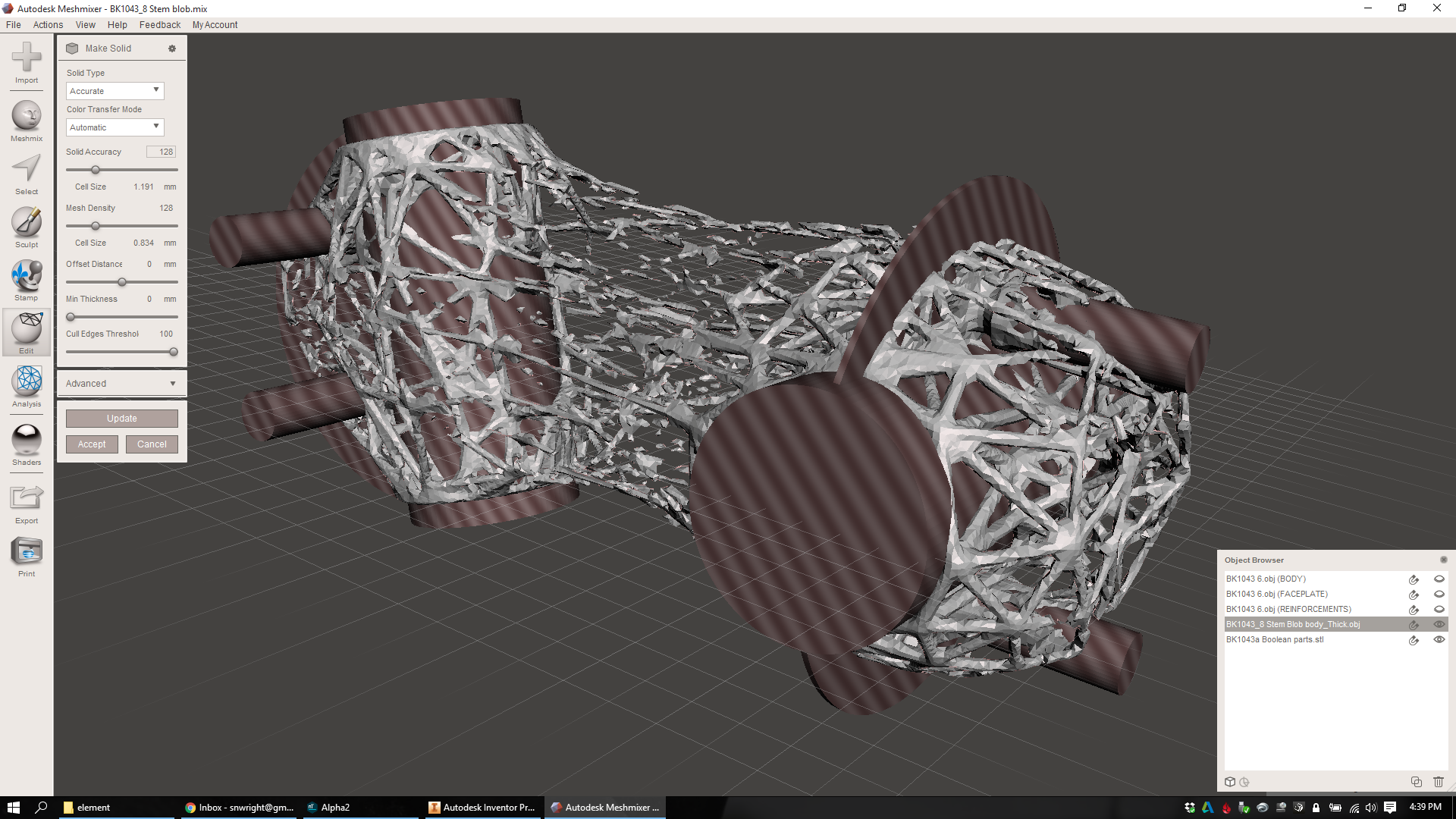
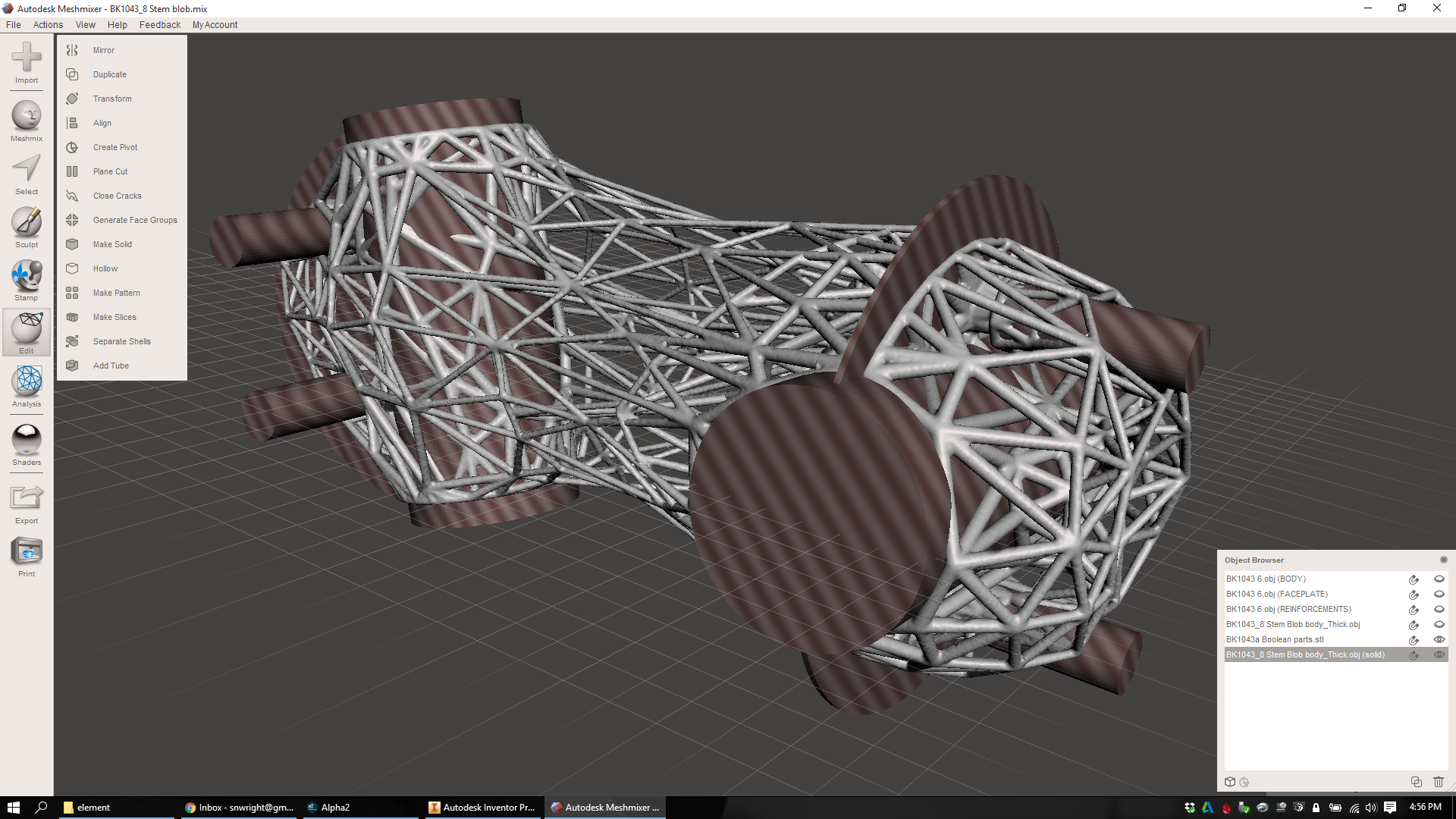
Now I've got a single lattice object that's fully solid and ready to have its mechanical features taken back out. Pretty rad. I combine the lattice and the mechanical features into one object and run "Make Solid" again, again at high density and accuracy:

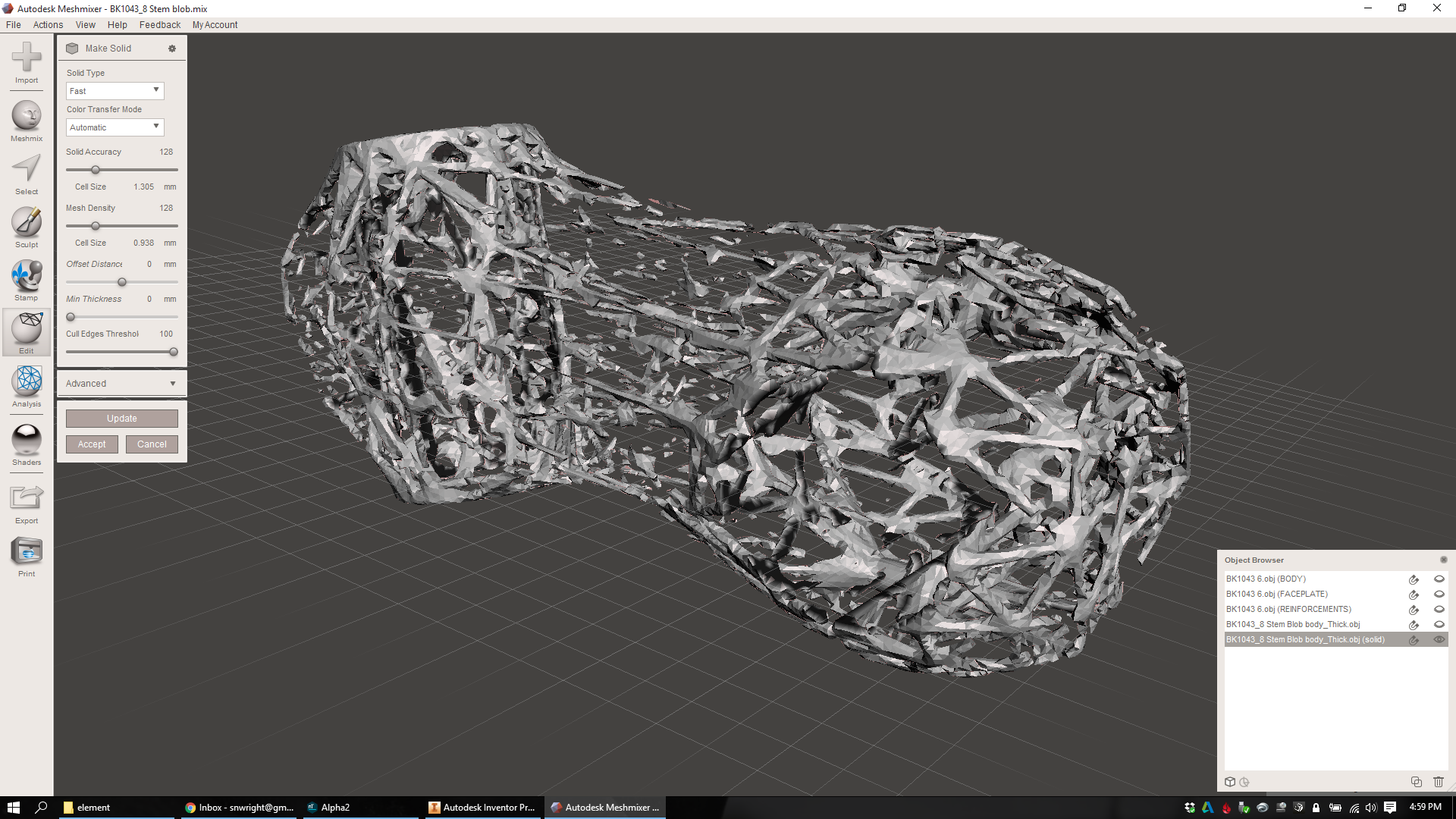
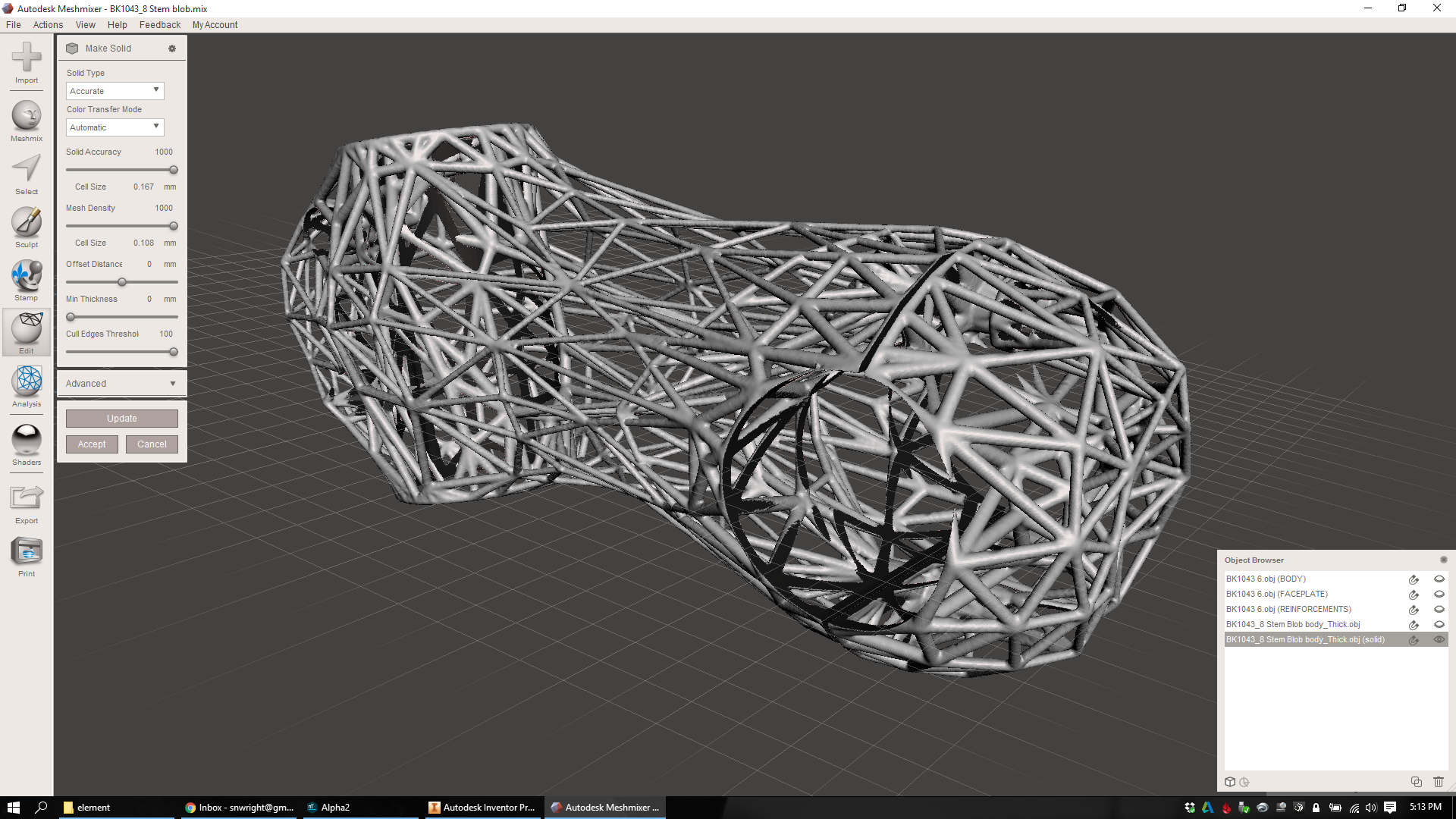
I select the result, run the Inspector tool, and fix any errors. Then I look around the lattice and evaluate it. Inevitably there are a bunch of areas that are cut off, thin, or chunky - places where the lattice was thin once the mechanical features were removed, and the meshing operation rounded over the resulting isthmus. Unfortunately, that's not something that I can go back and fix; I need to move individual nodes back in my original lattice in MeshMixer. But at least I know that now, and going back through the workflow actually isn't as painful as it sounds. And anyway, the part that I have now is actually pretty good:
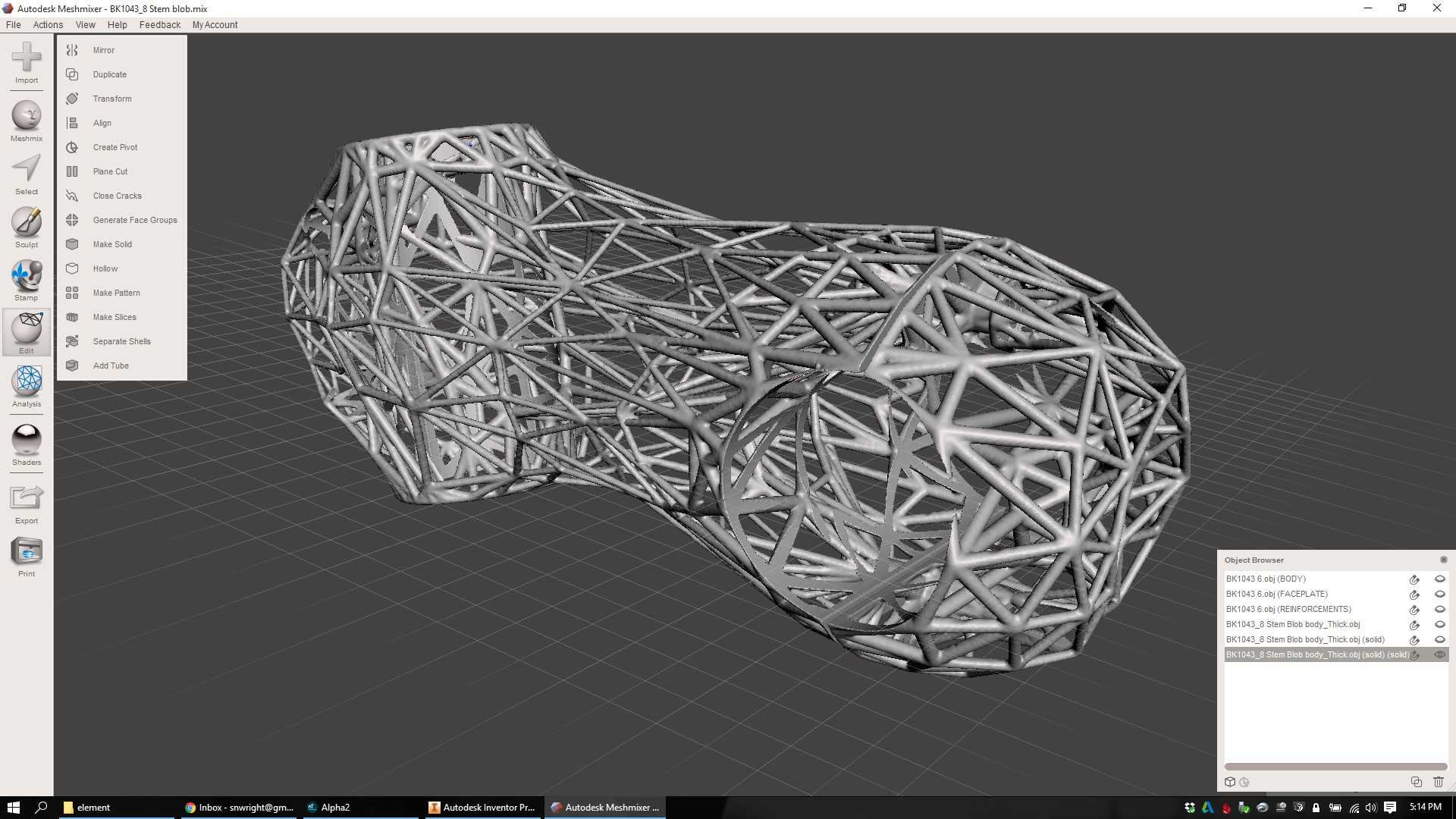
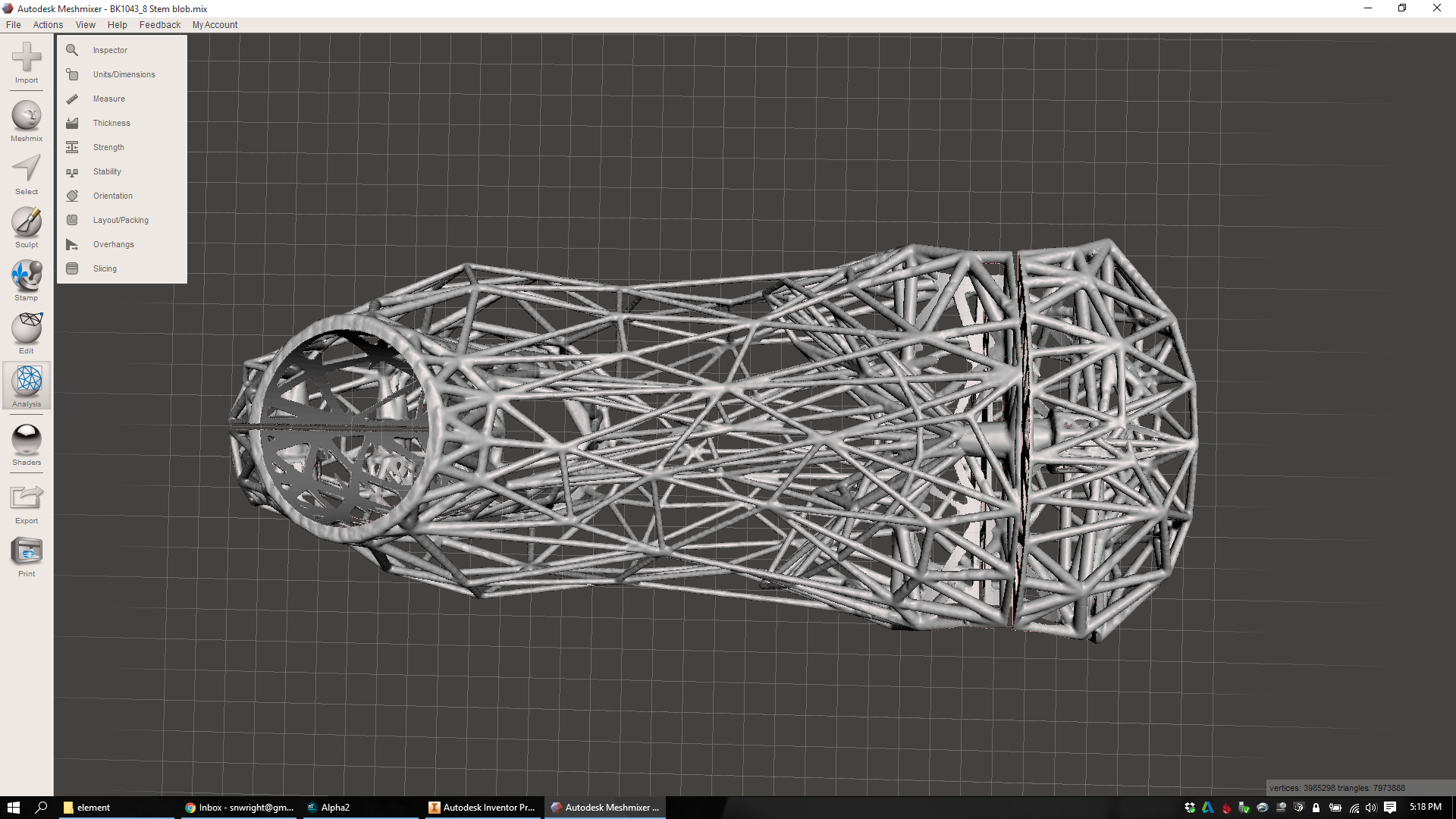
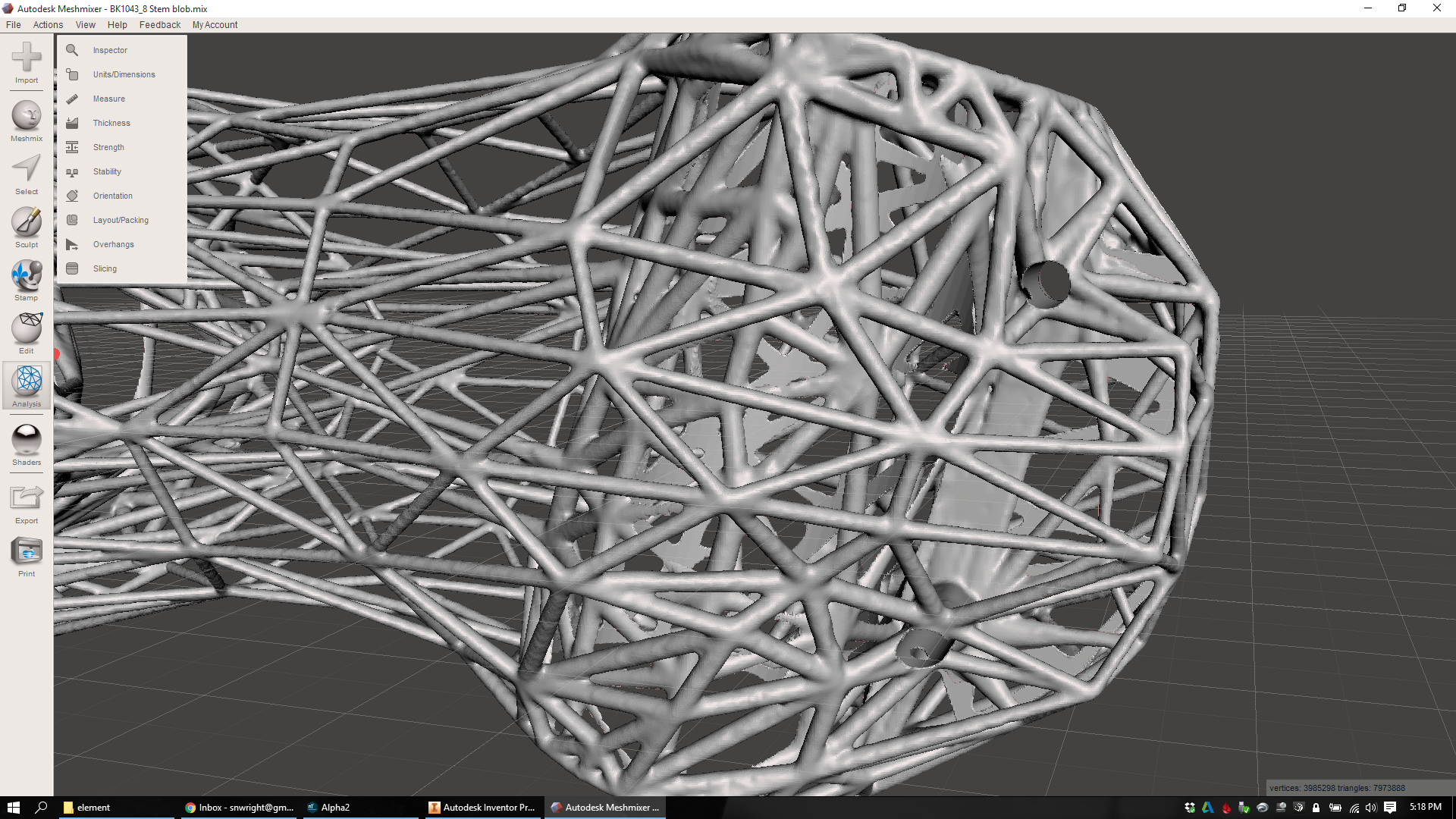
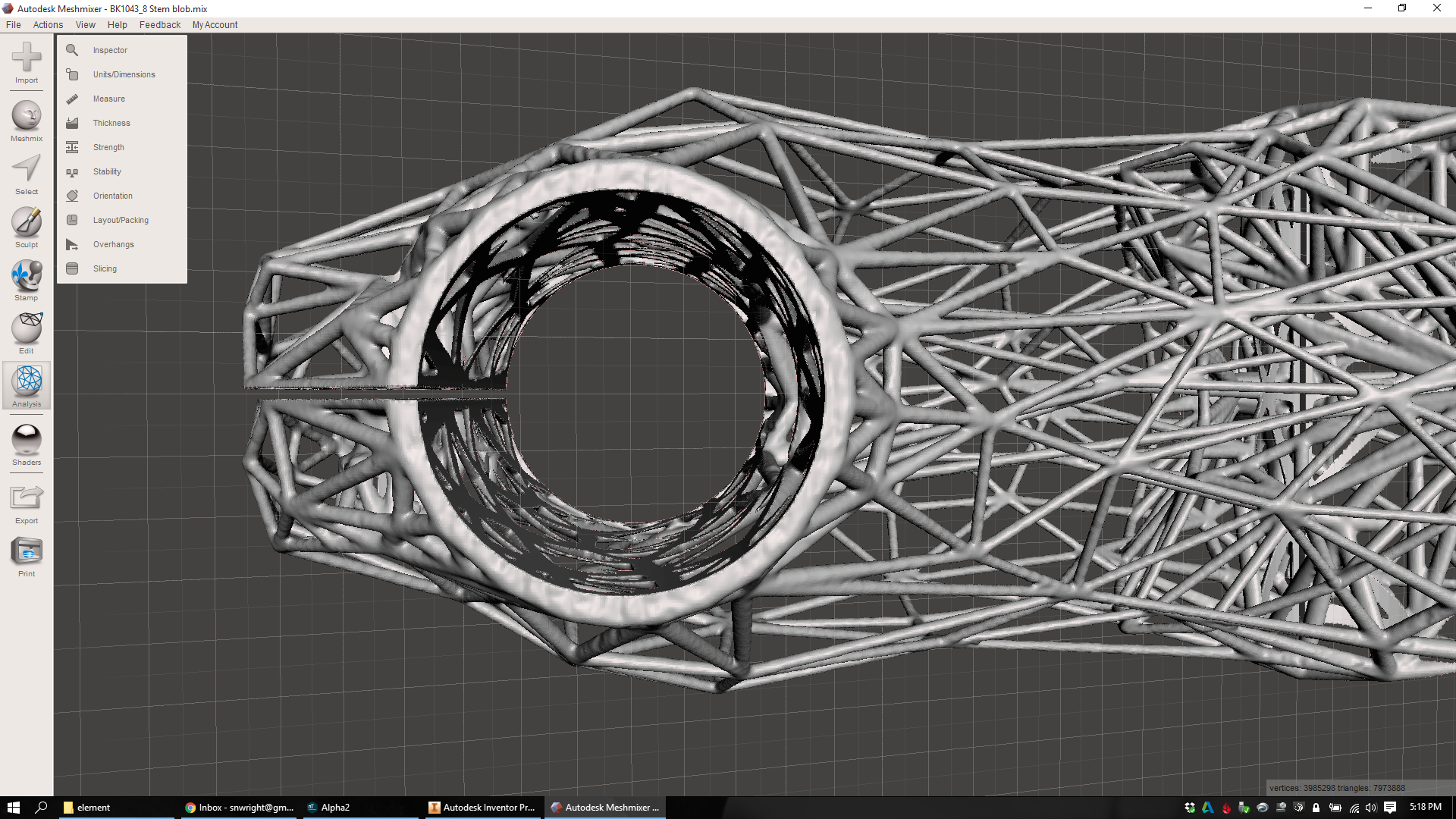
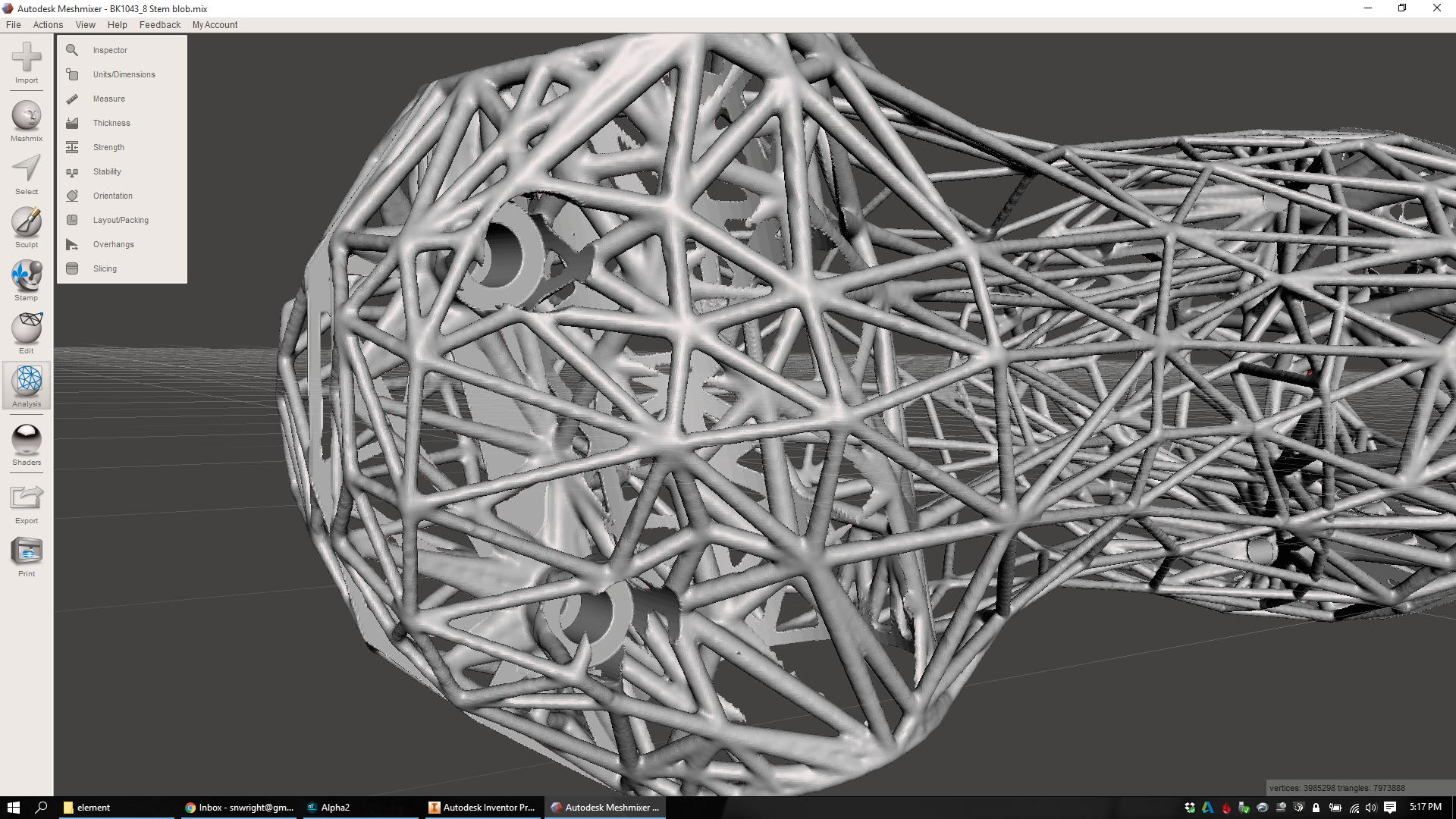
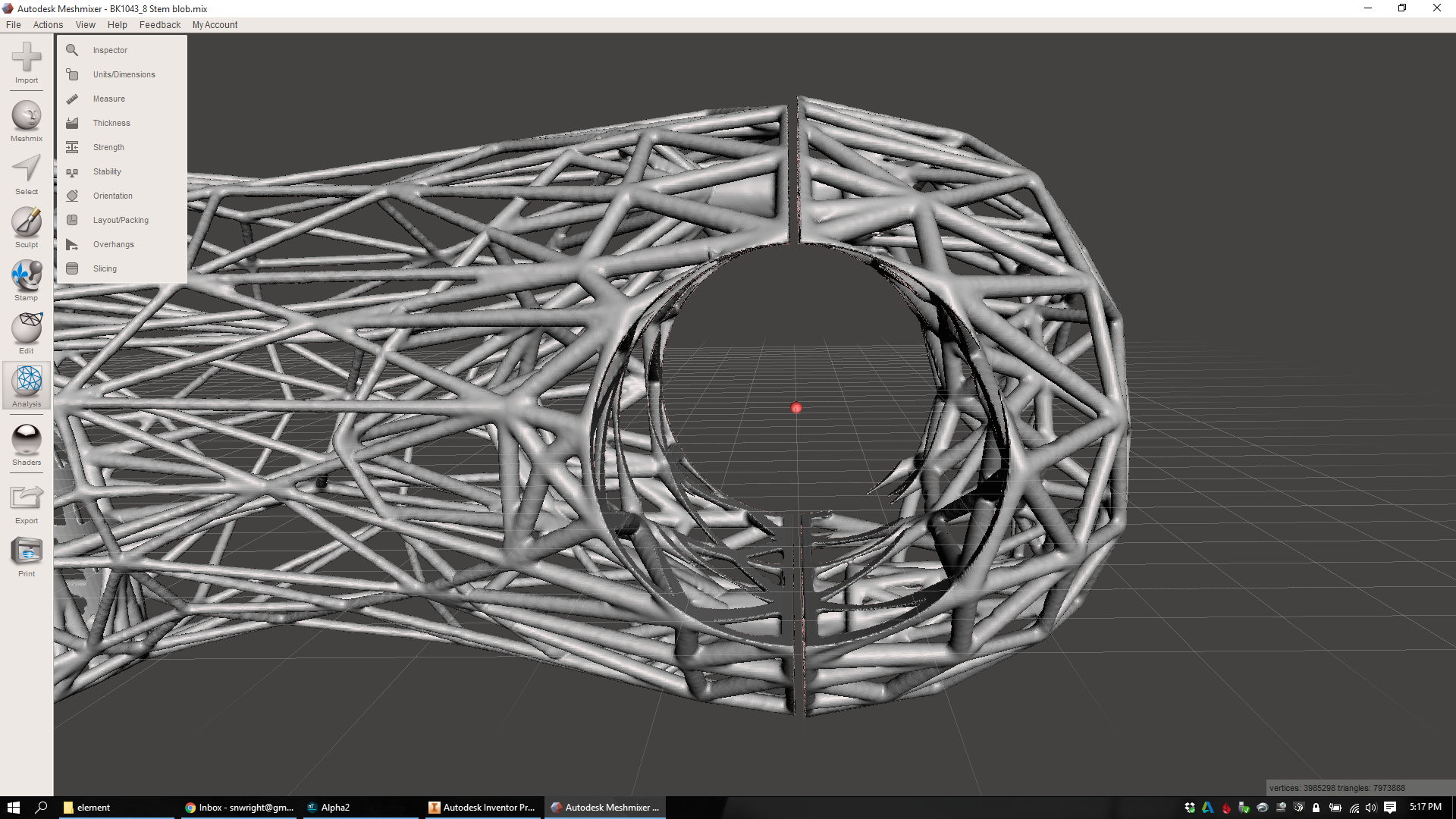
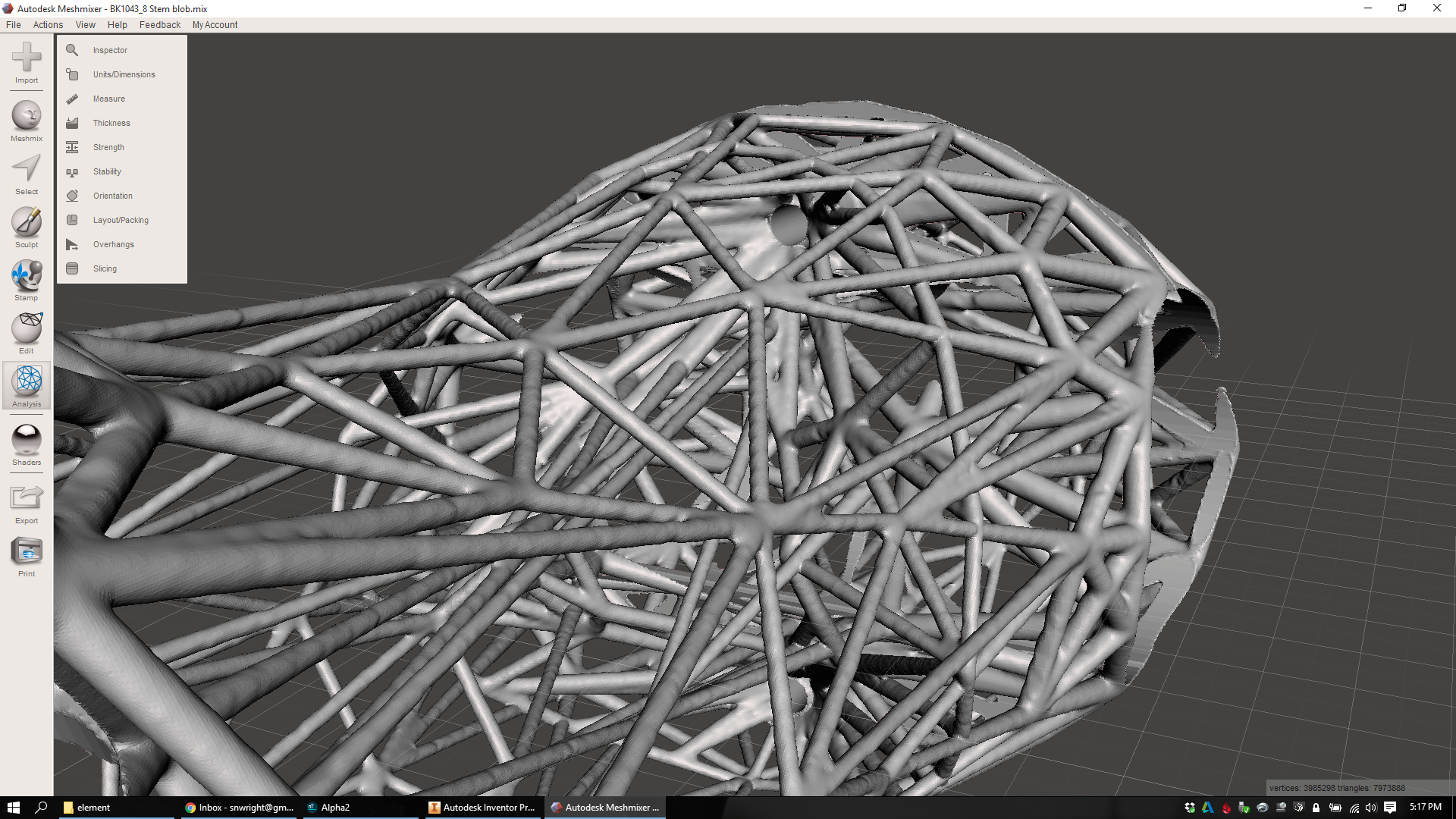
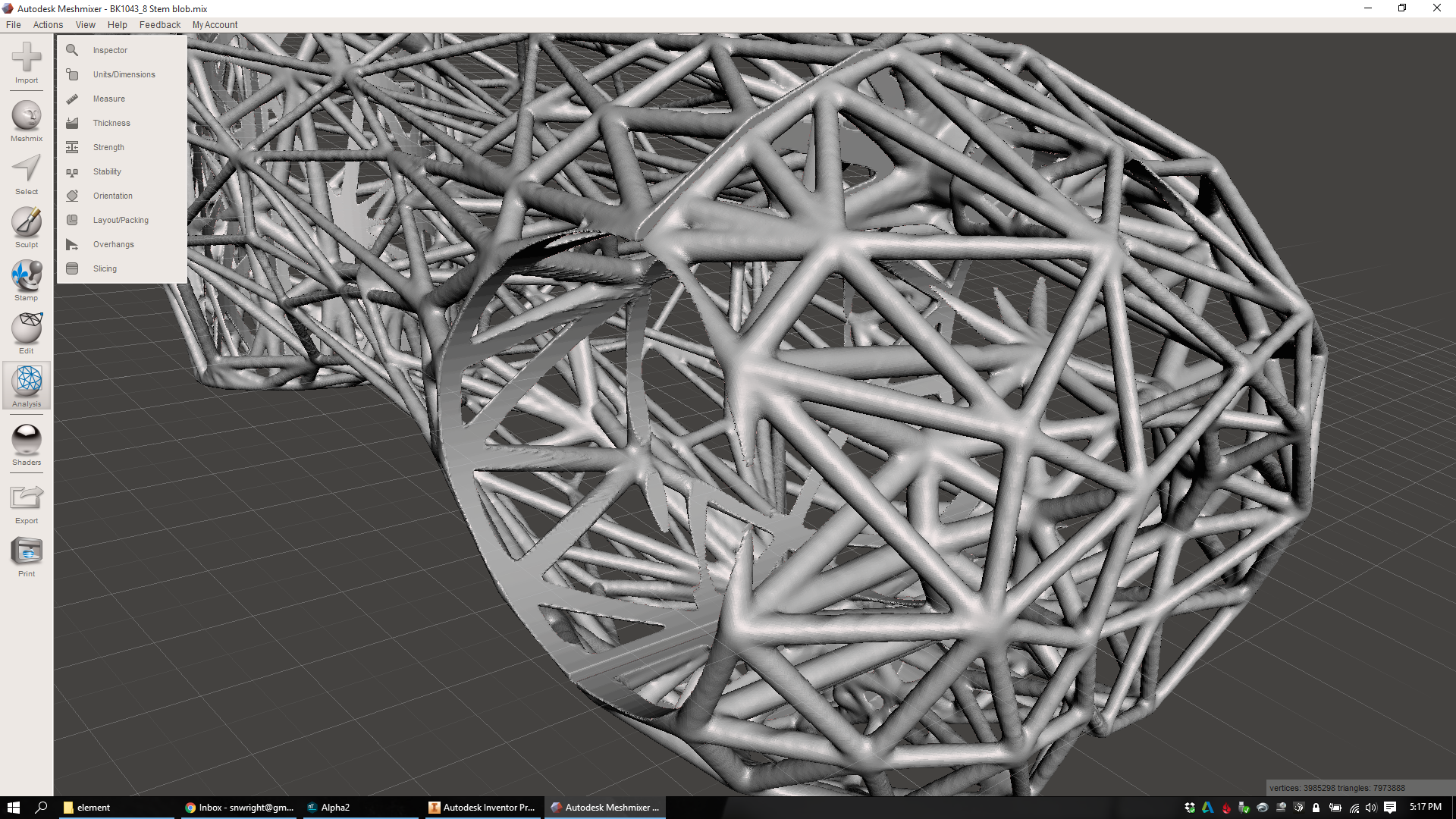
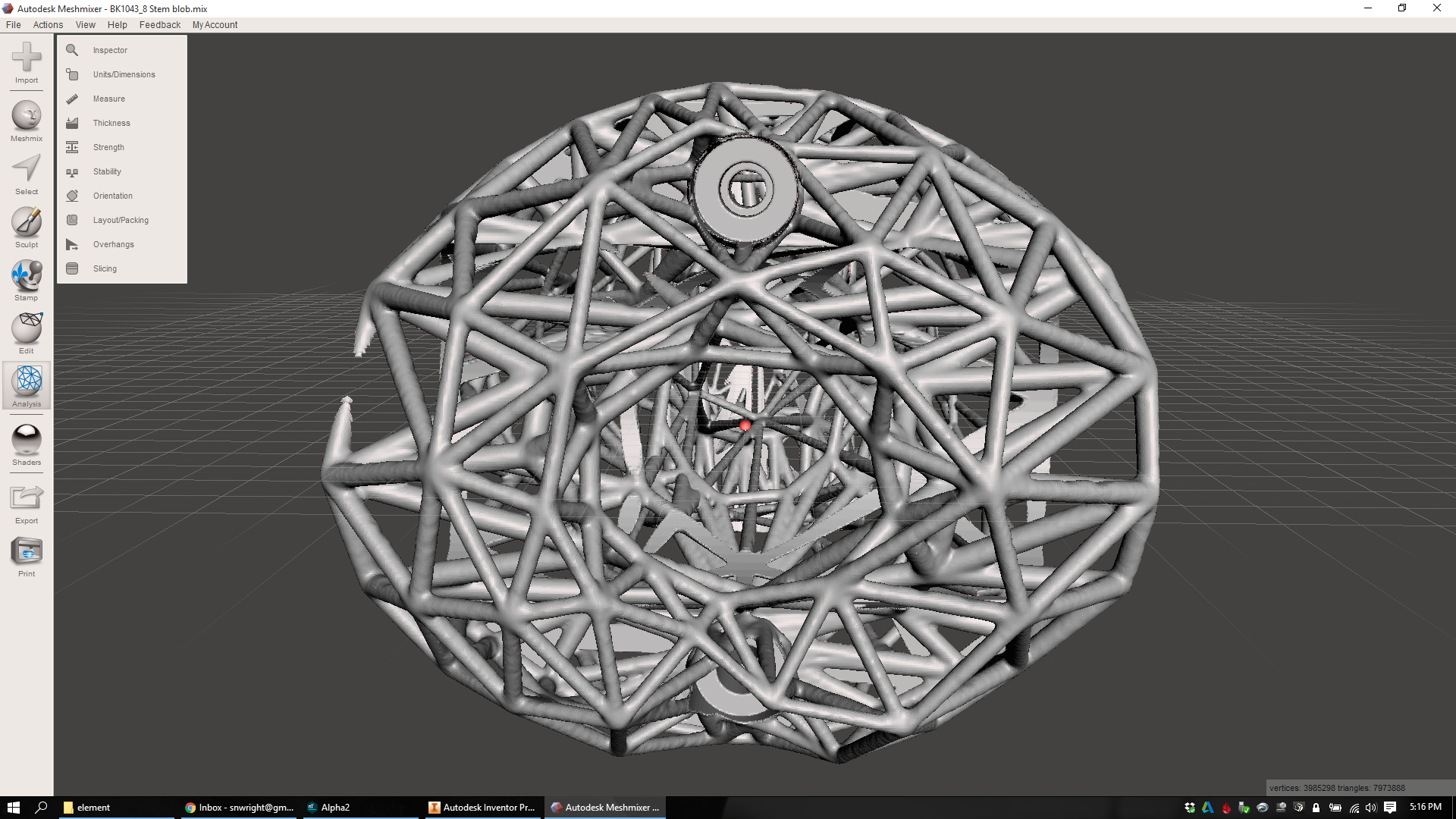
I should note here that I got a *lot* of help on the Boolean operations from Ryan Schmidt. Ryan also recorded a full video showing how to reintroduce the mechanical features even if you didn't have the ability to create them in Inventor. Although I went a slightly different route, there's a lot here that's super useful - and it shows the really powerful features that are built into MeshMixer:
Now that I've gone through the full process from start to finish, I see a few aspects of my design that still need some work. I also know that I still need to reduce the number of overhanging features in my design (which will probably be built on its end, with the handlebar side up). I'm also excited to test out the lattice utilities that are built into the most recent build of nTopology Element - especially in the area where the handlebar bolt reinforcements interface with the rest of the stem body. Bradley describes the process here:
I also, for what it's worth, need to do some actual FEA on my part. But by focusing on a repeatable workflow for even designing parts like this - and keeping a mind towards some basic manufacturability constraints - I've got something here that shows some promise. More soon :)